Hochratenfähiges Fügen von Bipolarplatten aus zwei Halbplatten (HP2BPP)
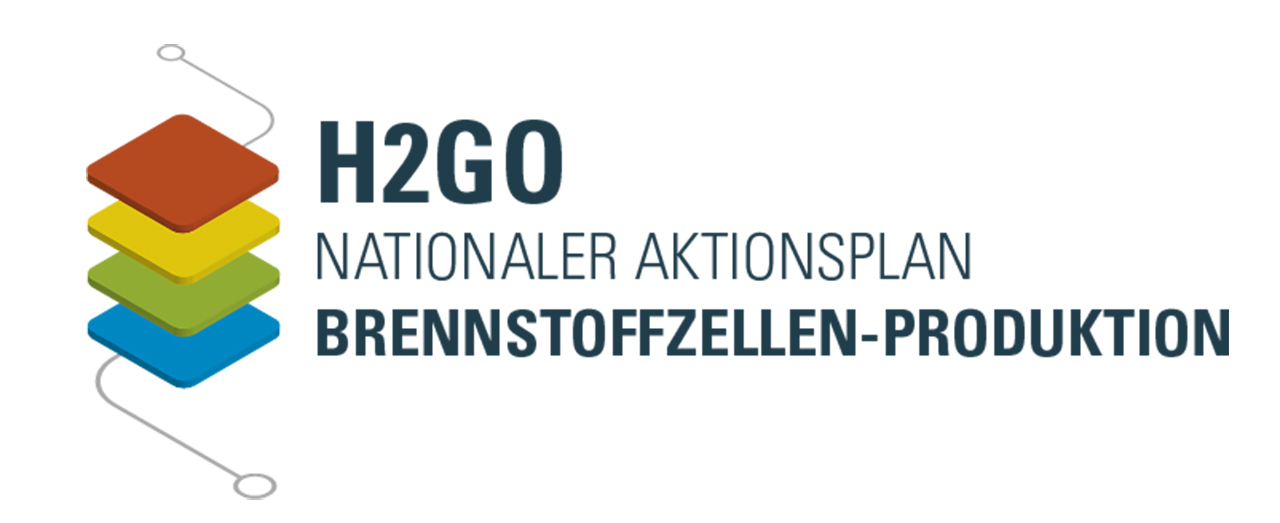
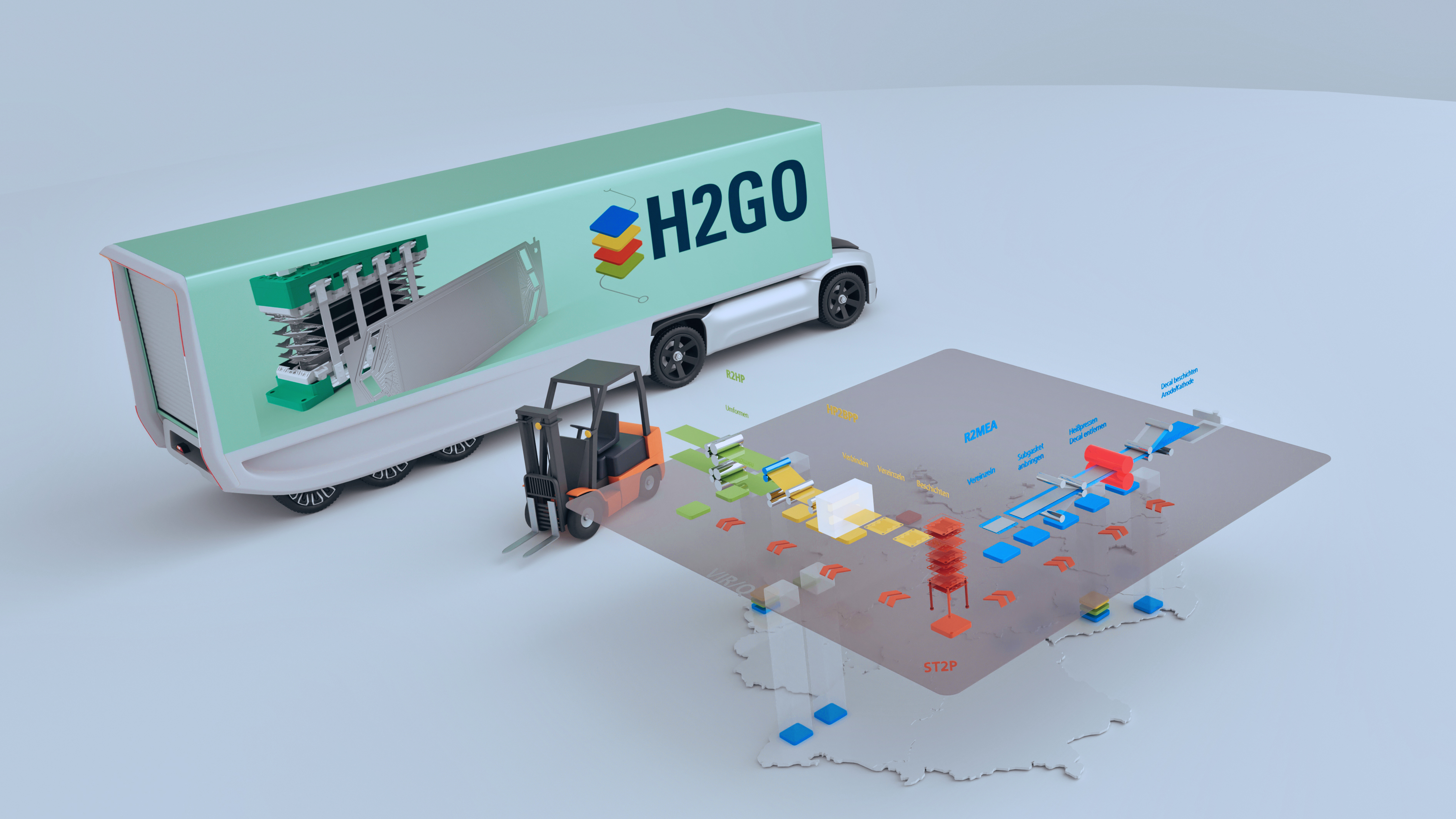
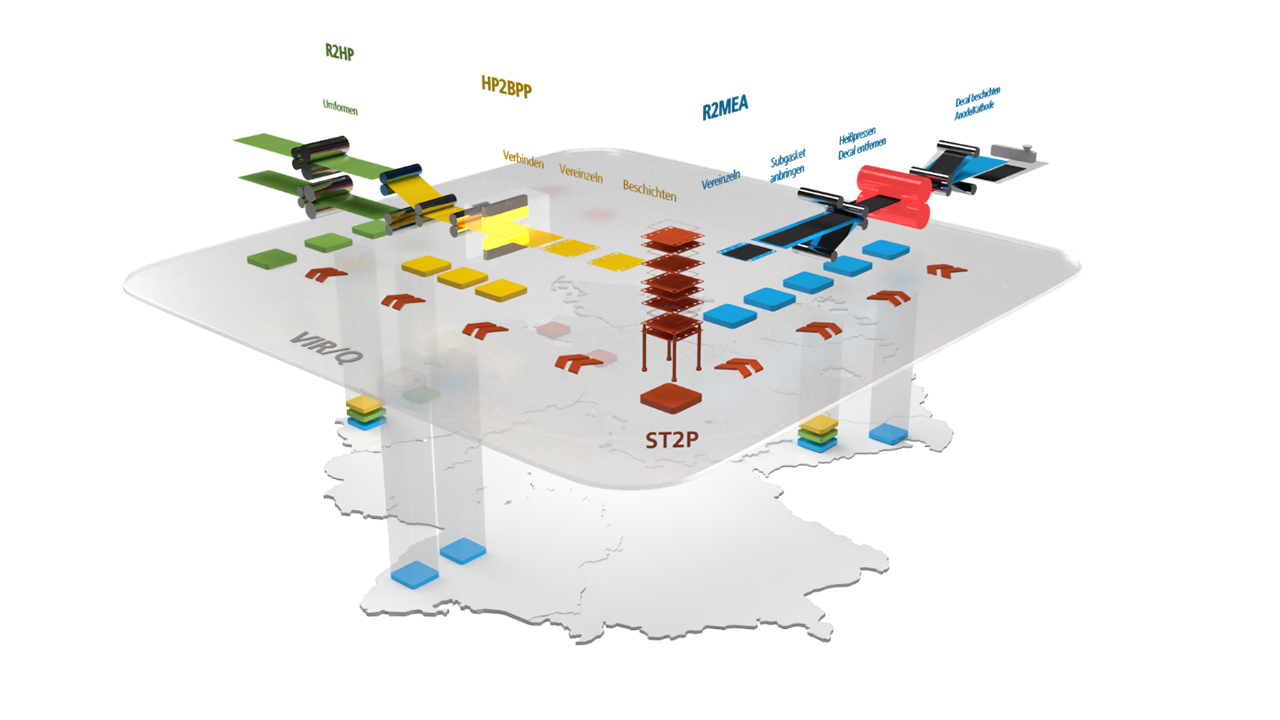
Projektbeschreibung
Das Verbundprojekt HP2BPP entwickelt innerhalb des H2GO Clusters die Technologien und Anlagen, die für eine hochratenfähige und gleichzeitig flexible Produktion von Bipolarplatten (BPP) für Brennstoffzellen zukünftig notwendig sind.
Ausgehend vom ganzheitlichen kontinuierlichen Prozessgedanken werden die durch den Verbund R2HP produzierten Halbplatten dem Fügeprozess zugeführt. Hierfür werden die notwendigen Entwicklungen vorangetrieben, die beim thermischen Fügen, Fügen durch Kleben, Oberflächenbeschichten, Separieren, Aktivieren, Reinigen und beim Bewerten/Prüfen der Komponente Bipolarplatte die geforderten Produktionsraten qualitätsgerecht ermöglichen.
Die einzelnen Produktionsmodule richten sich dabei in ihrem Forschungsschwerpunkten u. a. nach den technologischen Möglichkeiten der potenziellen Anwender, den sich aus dem genutzten Material ergebenden technologischen Randbedingungen sowie nicht zuletzt den prognostizierten marktseitigen Kostenforderungen. Übergreifende Zielstellung der Entwicklungen ist es, die Herstellung einer gefügten und qualitätsgerechten Bipolarplatte in deutlich weniger als einer Sekunde zu ermöglichen.
Anteil des Fraunhofer IWS
Kontinuierliches Inline-Fügen zu Bipolarplatten / Laserwalzschweißen mit Walzklebeprozess
Das Ziel besteht darin, erstmalig den R2R-Prozess des walzspaltbasierten Fügens zusammen mit der Klebtechnologie in einer entsprechenden Demonstrationsanlage zum Multistrahl-Hochgeschwindigkeitsfügen von BPP abzubilden. Hierfür wird sowohl das Multistrahl-Laserspaltschweißen als auch das Dichtkleben der BPP technologisch weiterentwickelt und für eine hochratenfähige Fertigung vorbereitet. Die Synchronisation der Prozessschritte im Zusammenhang mit dem Bandvorschub sind wesentliche Herausforderungen. Ein weiterer Schwerpunkt liegt auf der online Prozesskontrolle zur Qualitätssicherung. Im Ergebnis wird ein Anlagenprototyp zum Fügen als auch ein BPP-Demonstrator erstellt.
Zur Erfüllung dieser Aufgabenstellung wird neben der zwingenden Erweiterung bestehender systemtechnischer Komponenten, ein bestehendes Laserwalzplattiergerüst soweit ertüchtigt, dass Bandgeschwindigkeiten ≥ 30 m/min mit Bandbreiten bis zu 145 mm realisiert werden können.
Als Ergebnis wird sowohl eine erhebliche Steigerung der erzielbaren Taktzeiten zur Fertigung von BPP als auch Wirtschaftlichkeit durch signifikante Reduzierung von Ausschuss gegenüber derzeitigen Fügeverfahren ermöglicht. Mit Abschluss dieses Aufgabenpakets wird ein Technologiereifegrad von TRL5 bis TRL6 für das Teilmodul des walzspaltbasierten Multistrahl-Laserspaltschweißen mit kombiniertem Walzklebeprozess erreicht.
Kontinuierliches Beschichten für Bipolarplatten / Kontinuierliche Vakuumbeschichtung
Ziel ist die anlagen- und prozesstechnische Weiterentwicklung der Vakuumbeschichtung von einem Batch in einen hochratefähigen Bandbeschichtungsprozess. Hierfür wird ein bestehendes und erprobtes hocheffizientes Schichtsystem auf die Bandanlage (Bandgeschwindigkeit 10 m/min, Bandbreite 300 mm) übertragen. Eigene Wirtschaftlichkeitsberechnungen zum Vergleich von Batch- und Band-Prozessen, wie sie in diesem Projekt entwickelt werden, zeigten eine mögliche Reduktion der Beschichtungskosten um bis zu 90 % pro BPP durch eine Bandbeschichtung. Dies wurde für eine mögliche Ausbringung von ca. 2,5 Mio. BPP pro Jahr (Bandbreite 300 mm und Bandgeschwindigkeit 10 m/min) berechnet. Weiterhin wird ein Skalierungskonzept für Bandgeschwindigkeiten von 50 bis 100 m/min. bzw. breiteres Band und eine entsprechende Wirtschaftlichkeitsberechnung durchgeführt. Erwartet werden hierdurch zusätzliche Kosteneinsparungen. Ein weiteres Ziel ist die Entwicklung einer 100 % und vollflächigen KI-basierten Inline-Prozesskontrolle für die Bandbeschichtung auf einer Bandbreite von 300 mm.
Bei erfolgreichem Projektverlauf wird als Ergebnis sowohl eine erhebliche Kostenreduktion für Beschichtungen als auch eine Steigerung der Materialeffizienz durch Verringerung der notwendigen Schichtdicke erreicht. Das hierbei anvisierte Konzept ist geeignet, eine zukünftige Massenproduktion aufzubauen.
Kontinuierliches Inline-Austrennen und -Freischneiden von Bipolarplatten / Hochgeschwindigkeitsschneiden mittels CW-Lasern
Ziel ist die Weiterentwicklung der Schneid- und Trennverfahren zur kontinuierlichen Fertigung von BPP startend vom Technologiereifegrad 4 hin zum Technologiereifegrad 6. Im Ergebnis steht die Demonstration aller notwendigen trennenden Arbeitsschritte in der Herstellung von BPP mit mindestens der Prozessgeschwindigkeit vorgelagerter Prozessschritte. Der Demonstrator ermöglicht die virtuelle Verkopplung der Fertigungskette als auch die physische Vereinzelung der in vorangegangenen Prozessschritten hergestellter Halbzeuge mit den im Fertigungsdesign definierten Spezifikationen, sodass im Ergebnis hinsichtlich Qualität und Quantität bewertbare Halbzeuge vorliegen.