Generatives Laser-Pulver-Auftragschweißen
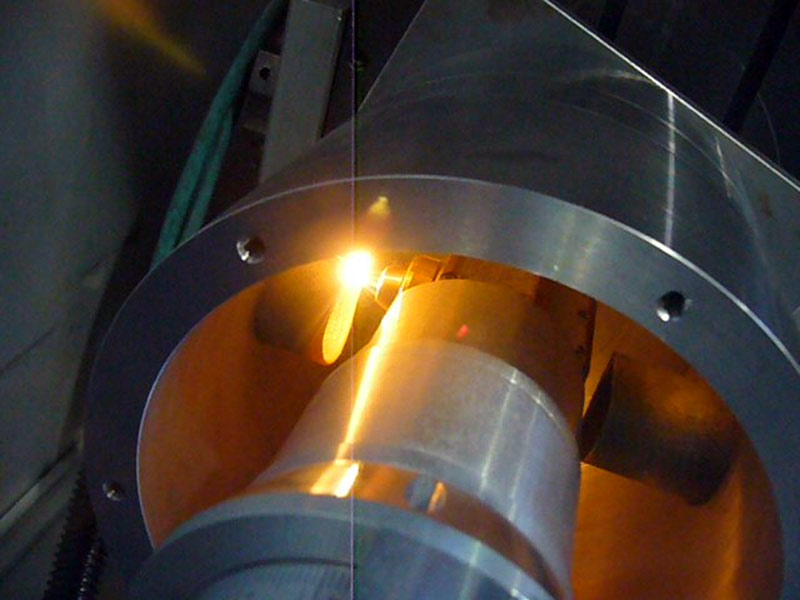
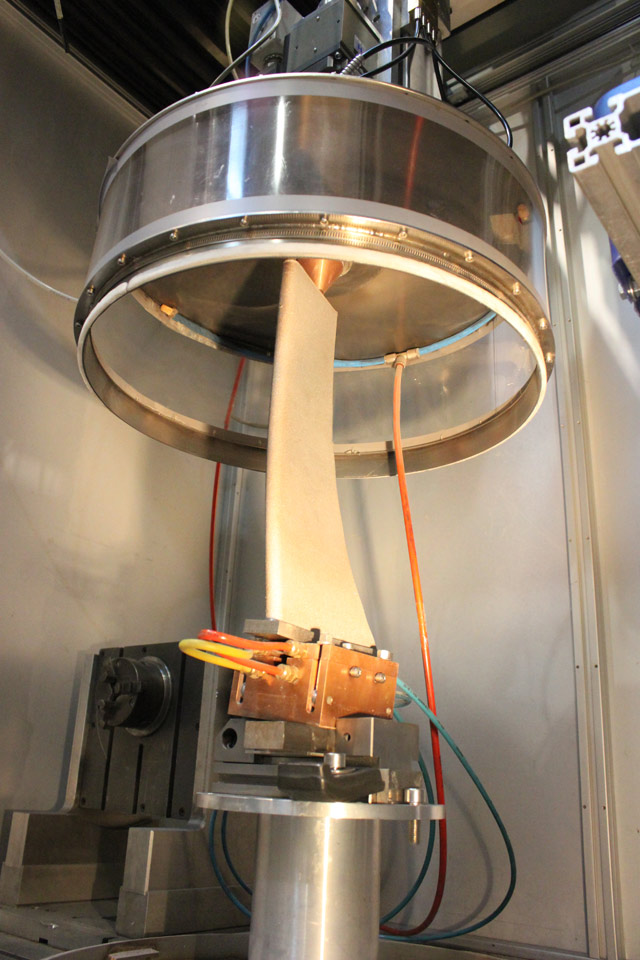
Auf der Basis von 3D-CAD-Datenmodellen werden dreidimensionale Metallstrukturen erzeugt, um Bauteile direkt zu fertigen, zu modifizieren oder zu reparieren. Die Bauteilgröße ist bei dieser Verfahrensvariante nicht limitiert. Die kleinste laterale Strukturauflösung beträgt 30 µm. Defektfrei verarbeitet werden können Stähle, Nickel- und Kobalt-Legierungen, Titan- und Aluminium-Leichtbauwerkstoffe sowie karbidische Komposite. Aktuell in der Entwicklung befinden sich drüber hinaus intermetallische Titan-Aluminide sowie Ni-Basis-Hochtemperaturwerkstoffe.