SNEAK PEEK: Erste Einblicke in den noch nicht veröffentlichten Jahresbericht 2020/2021
Innovationen durch hybride Fertigung in der Luft- und Raumfahrt
Hybride Fertigung bezeichnet die Kombination unterschiedlicher Fertigungsverfahren, um deren Vorteile zielgerichtet einzusetzen. Derartige Ansätze werden am Fraunhofer IWS mit besonderem Fokus auf additive Fertigungsverfahren verfolgt. Die Hybridisierung kommt dort zum Einsatz, wo – lokal und geometrisch begrenzt – Werkstoffe mit optimierten Eigenschaften notwendig sind: etwa in der Medizintechnik, dem Automobil- und Anlagenbau sowie der Luft- und Raumfahrt.
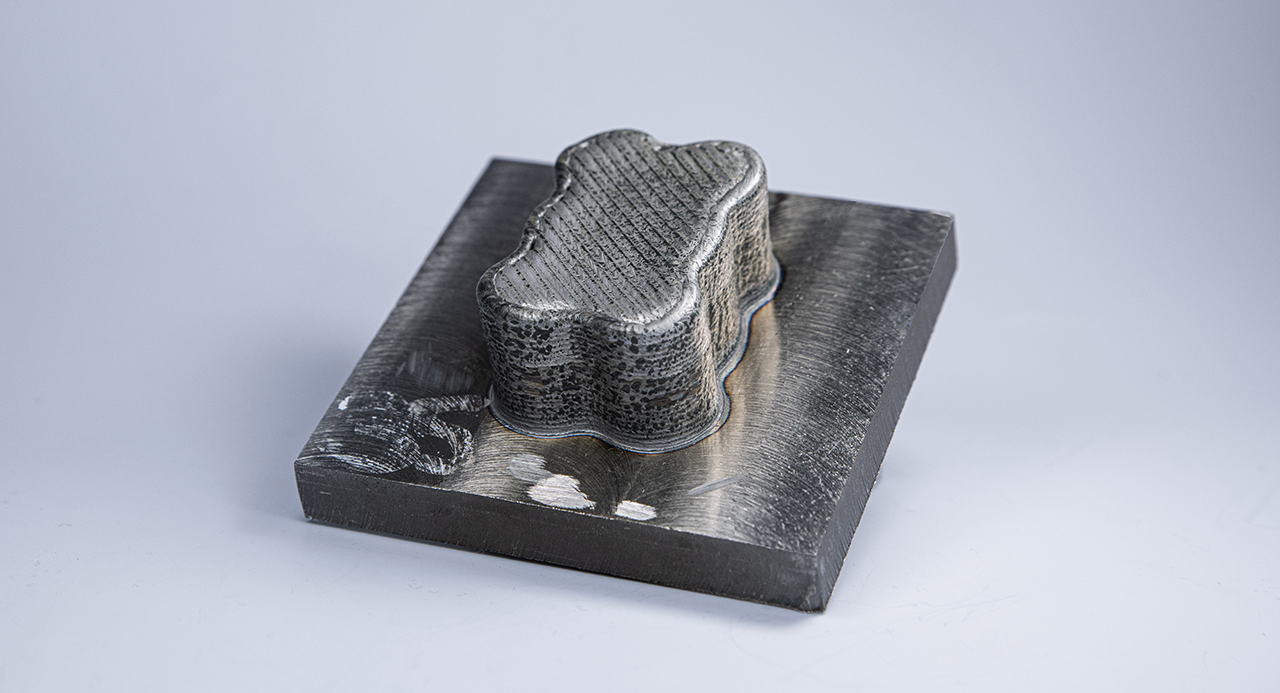
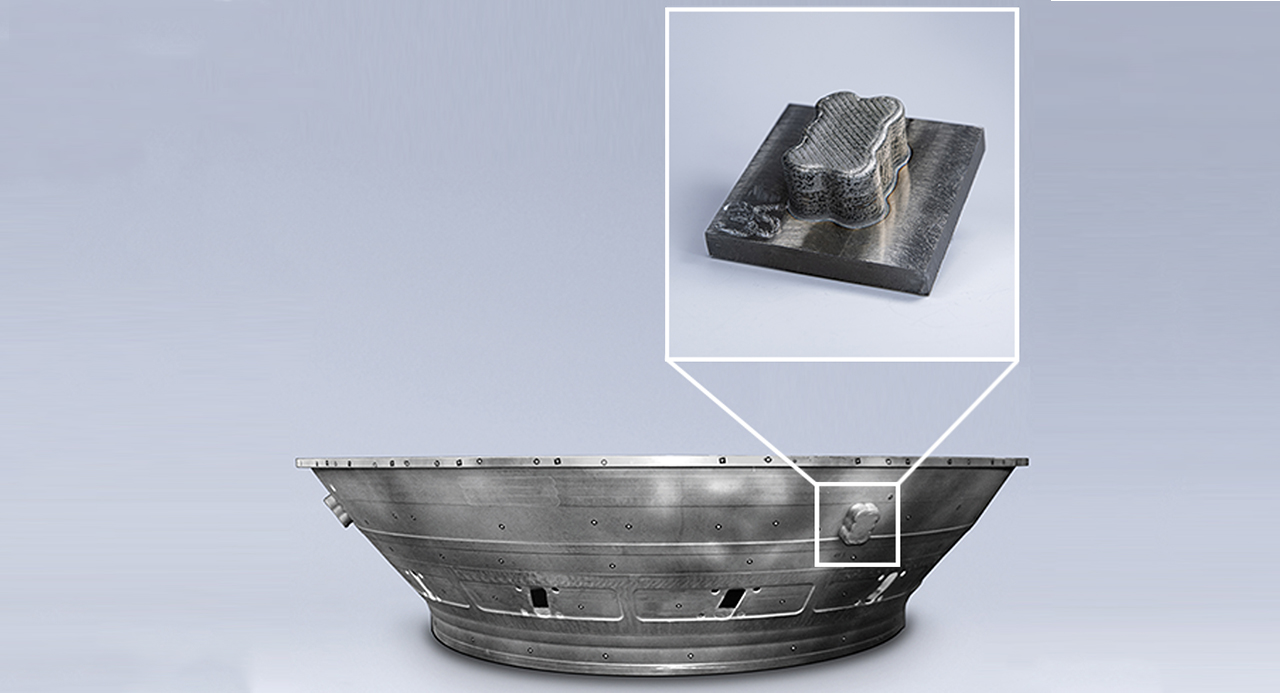
Im Projekt AGENT-3D_IMProVe entwickelte das Wissenschaftler-Team zusammen mit dem Projektpartner MTU Aero Engines die hybride Prozesskette aus dem additiven Laser-Draht-Auftragschweißen (LDA) und der konventionellen zerspanenden Bearbeitung. Es setzte sich zum Ziel, Halbzeugkosten einzusparen, indem es Materialvolumen reduzierte und Zerspanungszeiten verkürzte. So sollten Werkzeugkosten eingespart werden. Ein präziser additiver Aufbau mittels LDA auf dem konventionell hergestellten Substratkörper ermöglichte dies. Als drahtförmigen Zusatzwerkstoff verwendeten die Projektpartner eine Nickelbasislegierung (Inconel 718). »Diese zeichnet sich besonders durch ihre Festigkeit bei hohen Temperaturen und ihre hohe Korrosionsbeständigkeit gegenüber aggressiven Medien aus. Damit eignet sie sich besonders für thermisch stark beanspruchte Bereiche im Flugzeugturbinenbau«, berichtet Stefan Polenz. Zur Verarbeitung des Zusatzwerkstoffs nutzten die Wissenschaftler den am Fraunhofer IWS entwickelten koaxialen Prozesskopf COAXwire. Dieser verarbeitet drahtförmige Schweißzusatzwerkstoffe präzise und unabhängig von der Vorschubrichtung.
Den Start der Experimente bildete eine Parameterstudie zur Verarbeitung des Zusatzwerkstoffs auf artgleichen Substraten. Die so erzeugten Schweißspuren wurden mittels metallografischer Analysemethoden untersucht und bewertet. Die besten Parameter nutzten die Partner, um Volumenkörper für die Werkstoffcharakterisierung aufzubauen. Als entscheidende Erfolgskriterien lassen sich ein endkonturnaher, porenfreier Werkstoffauftrag und die gezielte Einstellung der geforderten Werkstoffeigenschaften nennen. Eine projektbegleitend aufgebaute intelligente Prozessüberwachung und Regelung unterstützte die reproduzierbare Probenherstellung.
Neuer Demonstrator mit geringerem Ausgangsmaterialvolumen entstanden
Auf Grundlage der erfolgreichen Vorversuche entwickelten die Forscher einen Demonstrator. Der Ingenieur Polenz berichet: »Dieser besteht aus einem konventionell zerspanend hergestellten Turbinengehäuse. Gefertigt wurde dieses aus einem Rohling mit kleinerem Materialvolumen als konventionell üblich. Für den konturnahen Aufbau sogenannter Boss-Strukturen nutzten wir anschließend das LDA-Verfahren.« Ein geringer lokaler Wärmeeintrag des LDA schaffte die Basis dafür, diese Struktur auf dem dünnwandigen Substrat mit einer Wandstärke von nur wenigen Millimetern erfolgreich verzugsarm aufzubauen. Die konturnahe Zerspanung und Wärmebehandlung testeten die Wissenschaftler bereits erfolgreich an Dummy-Bauteilen. Am finalen Demonstrator-Bauteil konnte bereits die Fertigung mehrerer Boss-Strukturen gezeigt werden. Die Die Nachbearbeitung steht noch aus.