SNEAK PEEK: Erste Einblicke in den noch unveröffentlichten Jahresbericht 2021/2022
ESA-ASPIRER: Aerospike-Triebwerk mit 6000 Newton Schub aus dem Pulverbett-3D-Drucker
Moderne Spritz-, Schweiß- und additive Fertigungstechnologien sollen dabei helfen, einem sehr sparsamen alternativen Raketenantrieb für lukrative Kleinsatelliten-Missionen zum Durchbruch zu verhelfen. Dabei handelt es sich um ein Aerospike-Triebwerk. Sie könnten den Treibstoffverbrauch bei vielen Raketenstarts um ein Drittel senken und damit die ökologische und finanzielle Bilanz der Raumfahrt verbessern.
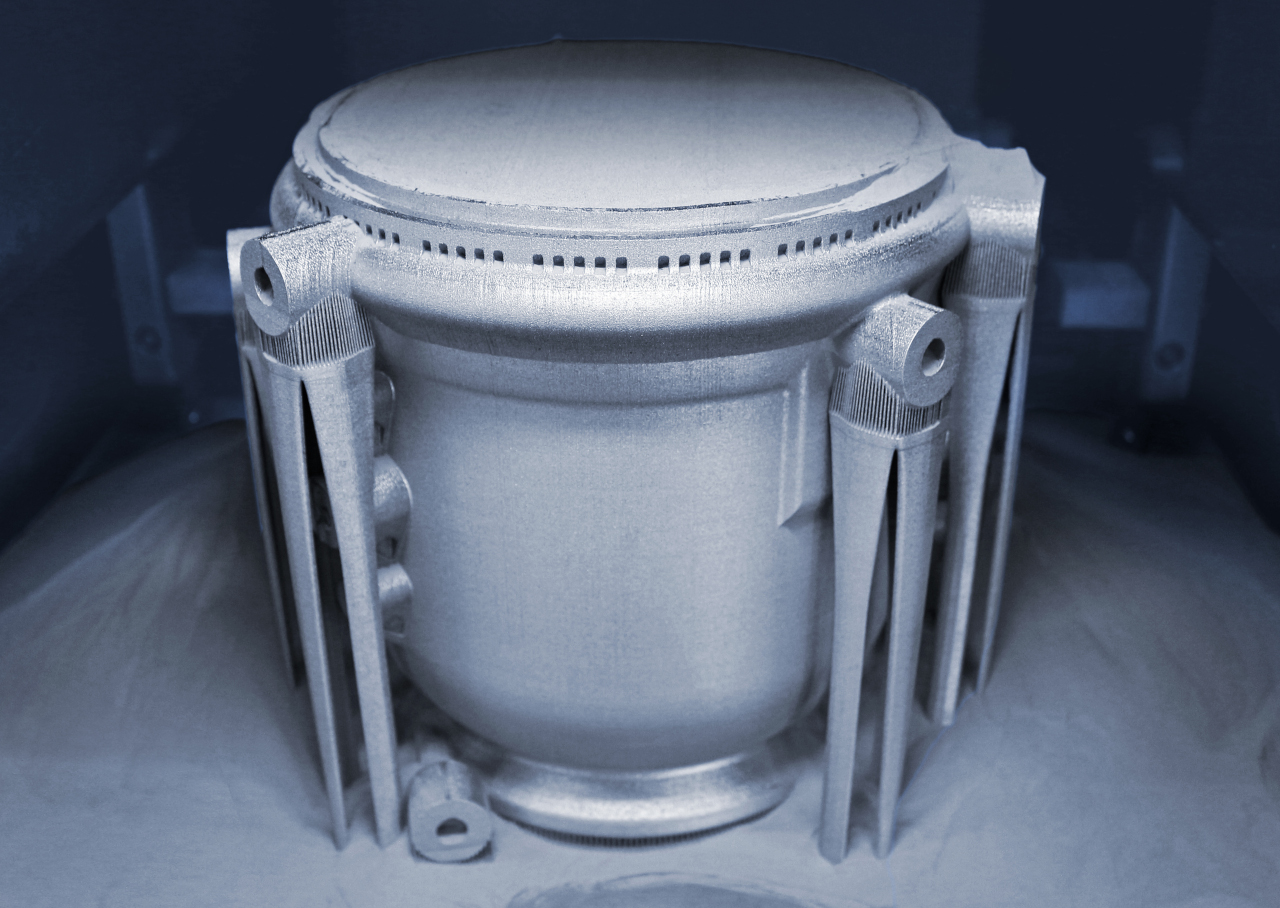
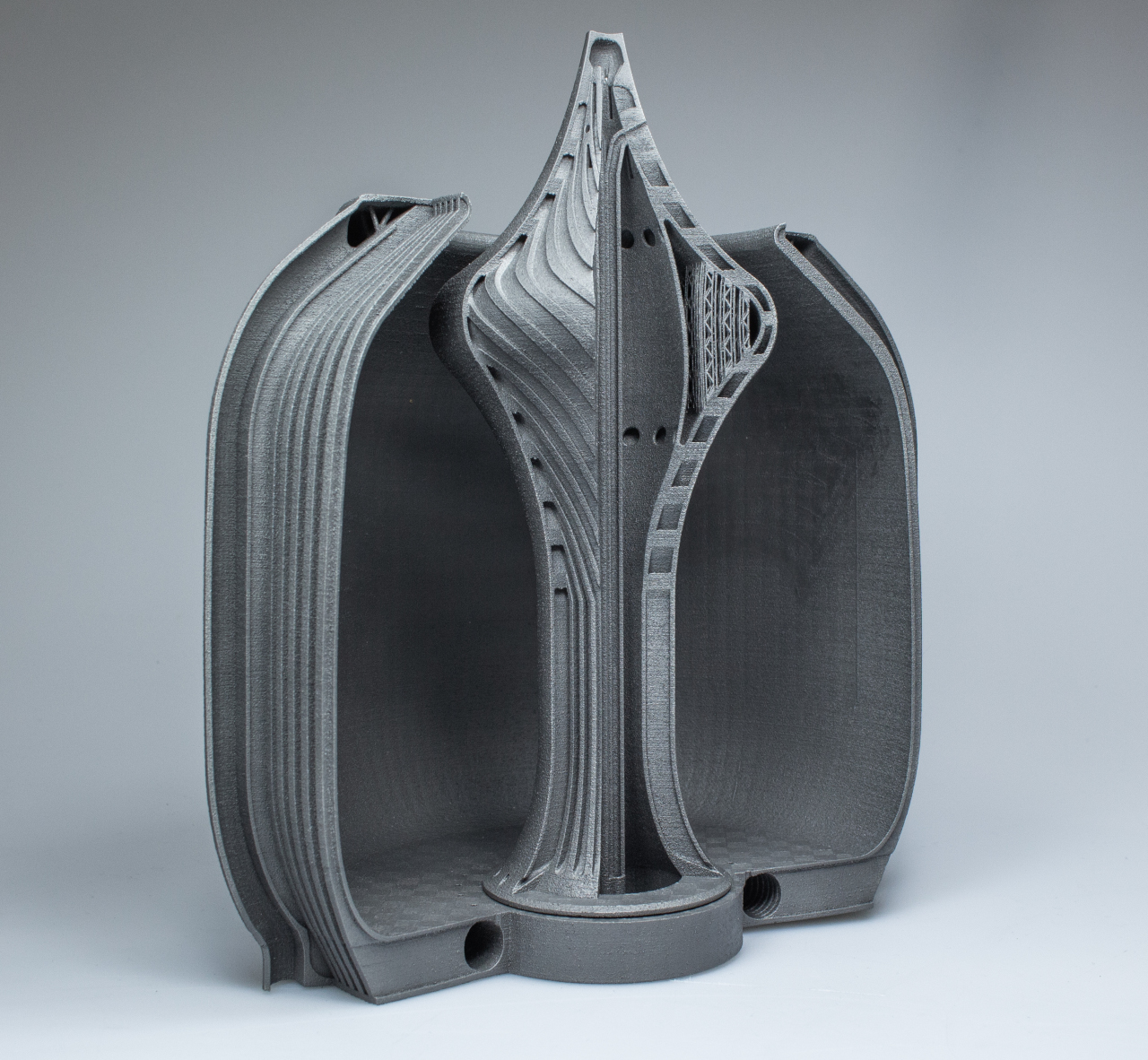
ESA-Forschungsprojekt entwickelt neue Raumfahrtantriebe
Im Gegensatz zu den klassischen glockenförmigen Raketendüsen bilden Aerospikes einen ringförmigen Spalt zwischen Stachel und Brennkammeraußenwand, um die heißen Abgase effizient in Schub umzuwandeln. Sie können sich dadurch besser an den Druck in verschiedenen Atmosphärenschichten anpassen und den Gas-Austrittsstrahl unabhängig vom Umgebungsdruck nahe an der idealen Form halten. Erdacht wurden Aerospikes bereits vor über 60 Jahren. Ihr praktischer Einsatz scheiterte aber an ihrer Komplexität und an der anspruchsvollen Fertigung. Denn mit traditionellen Verfahren lassen sich die komplexen inneren Kühlkanäle für solche Triebwerke kaum erzeugen. Das Institut für Luft- und Raumfahrttechnik (ILR) der TU Dresden und das Fraunhofer IWS arbeiten seit 2016 eng zusammen und haben bereits 2019 in einem Kooperationsprojekt ein 500 Newton starkes Aerospike-Triebwerk ausgelegt, gefertigt und getestet. Jedoch zeigten sich noch Probleme beim Kühlsystem und in der Treibstoff-Einspritzung. Seit 2020 fördert die europäische Raumfahrtagentur ESA das Projekt »AeroSPIke Rocket Engine Realisation« (ASPIRER). Damit geht die Kooperation von Forschenden des Fraunhofer IWS mit dem ILR, dem »Space Technologies Center – Lukasiewicz Research Network« aus Warschau und der ArianeGroup in die nächste Runde.
Einsatz von Laser zum Generieren und Fügen
Samira Gruber, Alex Selbmann und Michael Müller aus der Abteilung Additive Fertigung nutzen das pulverbettbasierte Laserstrahlschmelzen für die Fertigung der zwei Kernkomponenten Stachel und Brennkammeraußenwand. Die Laseranlage schmilzt dafür eine Nickel-Basis-Superlegierung im Metallpulverbett auf und erzeugt Schicht für Schicht die Bauteile. Wichtige Anschlussflächen werden mechanisch nachbearbeitet und die Injektorbohrungen erodiert, um notwendige Toleranzen einzuhalten. Danach erhalten die Teile in der Gruppe Thermisches Spritzen an den thermisch beanspruchten Oberflächen eine keramische Hitzeschutzschicht. Sie verhindert, dass das Kernmaterial später durch die heißen Gase beim Start und während der Flugphase schmilzt. Schließlich verschweißt ein weiteres Team am Fraunhofer IWS den Spike und den Flansch mit einem Laser. Anfang 2022 soll das Triebwerk fertig sein. Im Frühjahr 2022 wollen die Partner in Polen eine umfangreiche Testkampagne starten.
Rückblick Hannover Messe 2021: Additiv gefertigtes Raketentriebwerk mit Aerospike-Düse – vom Konzept bis zur Realisierung
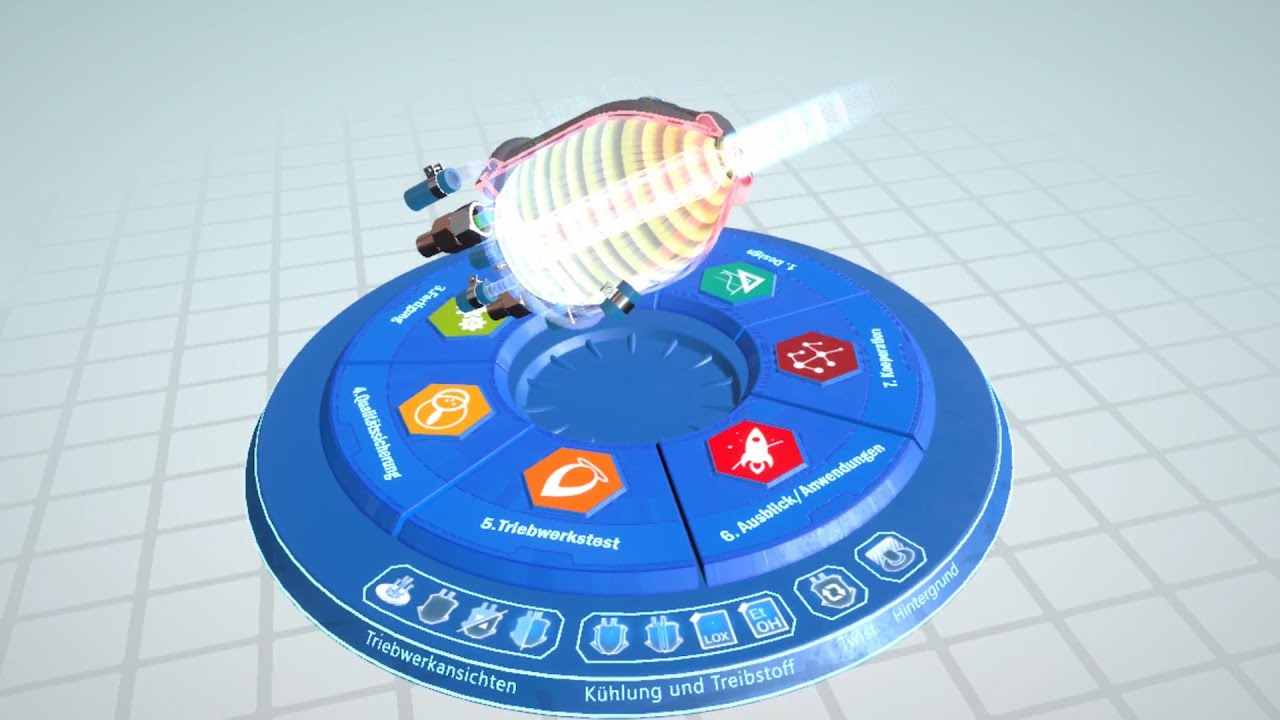
Datenschutz und Datenverarbeitung
Wir setzen zum Einbinden von Videos den Anbieter YouTube ein. Wie die meisten Websites verwendet YouTube Cookies, um Informationen über die Besucher ihrer Internetseite zu sammeln. Wenn Sie das Video starten, könnte dies Datenverarbeitungsvorgänge auslösen. Darauf haben wir keinen Einfluss. Weitere Informationen über Datenschutz bei YouTube finden Sie in deren Datenschutzerklärung unter: https://policies.google.com/privacyVideo: Additiv gefertigtes Raketentriebwerk mit Aerospike-Düse für Microlauncher: von Konzeptstudien bis zum Probebetrieb (YouTube)