Additive Fertigung einer optischen Bank für das neue ATHENA-Weltraumteleskop
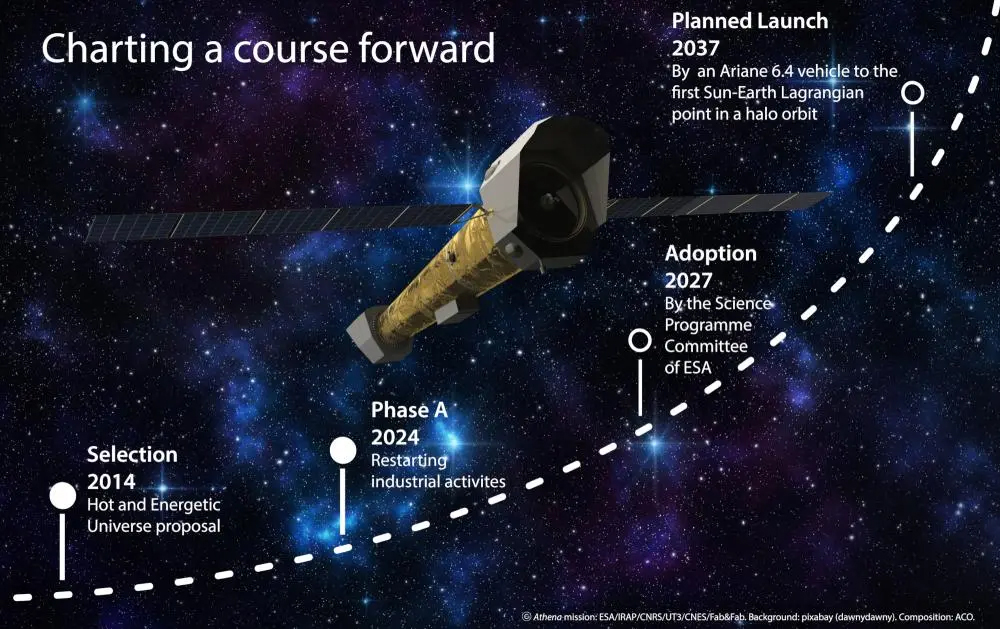
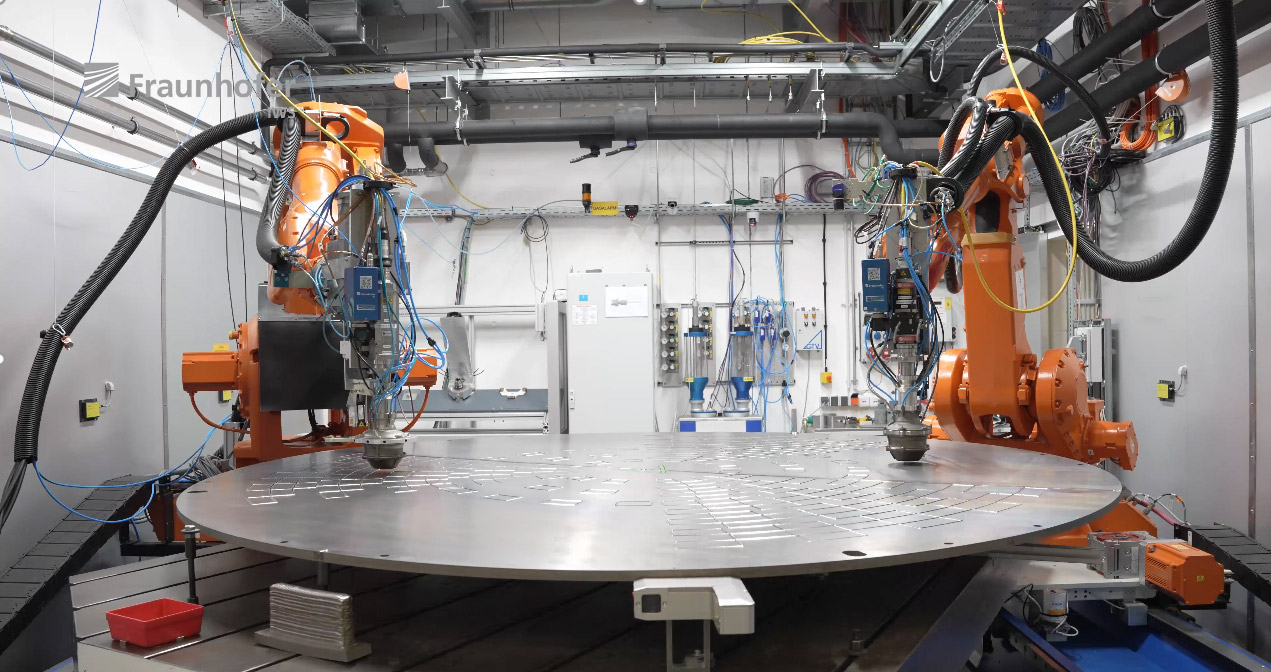
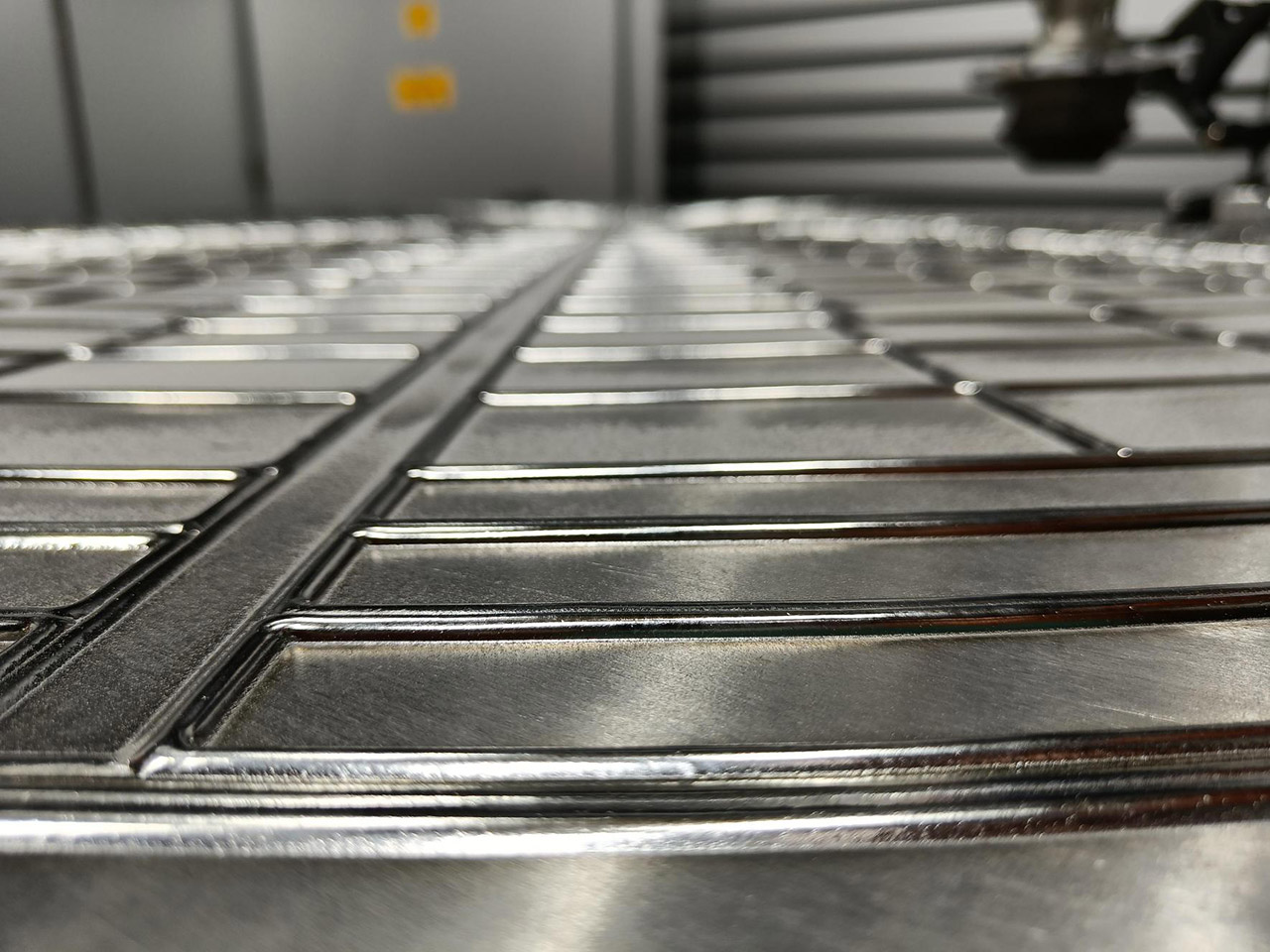
Motivation
Die Large Class Science Mission NewATHENA, die von der Europäischen Weltraumorganisation (ESA) im November 2023 neu aufgesetzt wurde, soll das heiße und energiereiche Universum mit Hilfe modernster Röntgentechnologie erforschen. Die Schlüsselkomponente des Teleskops werden Hunderte von SPO-Spiegelmodulen (Silicon Porous Optics) sein, die in einer optischen Bank mit einem Durchmesser von etwa 2,7 Metern angeordnet sind. In Anbetracht der Gesamtgröße, der empfindlichen Zellstruktur und der Seitenverhältnisse in Kombination mit den materialbedingten Herausforderungen von Ti6Al4V ist die additive Fertigung mittels Laser-Auftragschweißen eine vielversprechende Alternative zur konventionellen Verarbeitung.
Ziele und Vorgehen
Erste Forschungsaktivitäten im Auftrag der Europäischen Weltraumorganisation befassten sich mit der Skalierung und Parallelisierung von Fertigungsanlagen und der grundsätzlichen Machbarkeit eines hybriden Ansatzes, der Laser-Auftragschweißen und Fräsen kombiniert. Ausgehend von der Systementwicklung für die Fertigungsanlage erfolgte eine ganzheitliche Betrachtung verschiedener Entwicklungsschritte. Anschließend wurde im Fraunhofer IWS eine repräsentative optische Bank (Durchmesser 1,5 Meter) gefertigt. Die gewonnenen Erkenntnisse führten zu umfangreichen Anpassungen des Designs, des Prozesses, der Fertigungsstrategie und der Handhabung der Teile, um grundlegende Herausforderungen wie Verformung und Eigenspannungen zu bewältigen.
Innovationen und Perspektiven
Darüber hinaus wurde ein neuartiger Ansatz für eine lokale Abschirmung des Auftragschweißprozesses integriert, der die Versprödung von Titanlegierungen durch die Bildung der sogenannten »Alpha-Phase« aufgrund von Sauerstoffaufnahme verhindert. Die Eignung der entwickelten Technologien und Arbeitsabläufe für die NewATHENA-Mission wird nun durch die Herstellung eines zweiten repräsentativen, 2,7 Meter großen Prototyps in Originalgröße nachgewiesen. Die neuartige Fertigungsprozesskette, die geometrische Komplexität sowie die enorme Größe des Titanbauteils sind weltweit einzigartig.