Neuer Kaltwandofen am Fraunhofer IWS bietet sauberen Prozess und eröffnet größere Materialvielfalt
Sintern und Entbindern in einer Anlage
Das Fraunhofer-Institut für Werkstoff- und Strahltechnik IWS erweitert sein Anlagenportfolio, um seine Kompetenzen auf dem Forschungsgebiet des Additive Manufacturing voranzutreiben. Neben einem Binder-Jetter steht nun auch ein neuer Kaltwandofen zur Verfügung, der die zwei Nachbearbeitungsschritte Entbindern und Sintern in einer Anlage durchführen kann. Zusammen mit dem Binder Jetter bildet das Dresdner Institut nun den kompletten Herstellungs- und Bearbeitungsprozess von Bauteilen ab und stellt ihn interessierten Anwendern und Forschern zur Verfügung, die sich mit diesem additiven Herstellungsprozess beschäftigen.
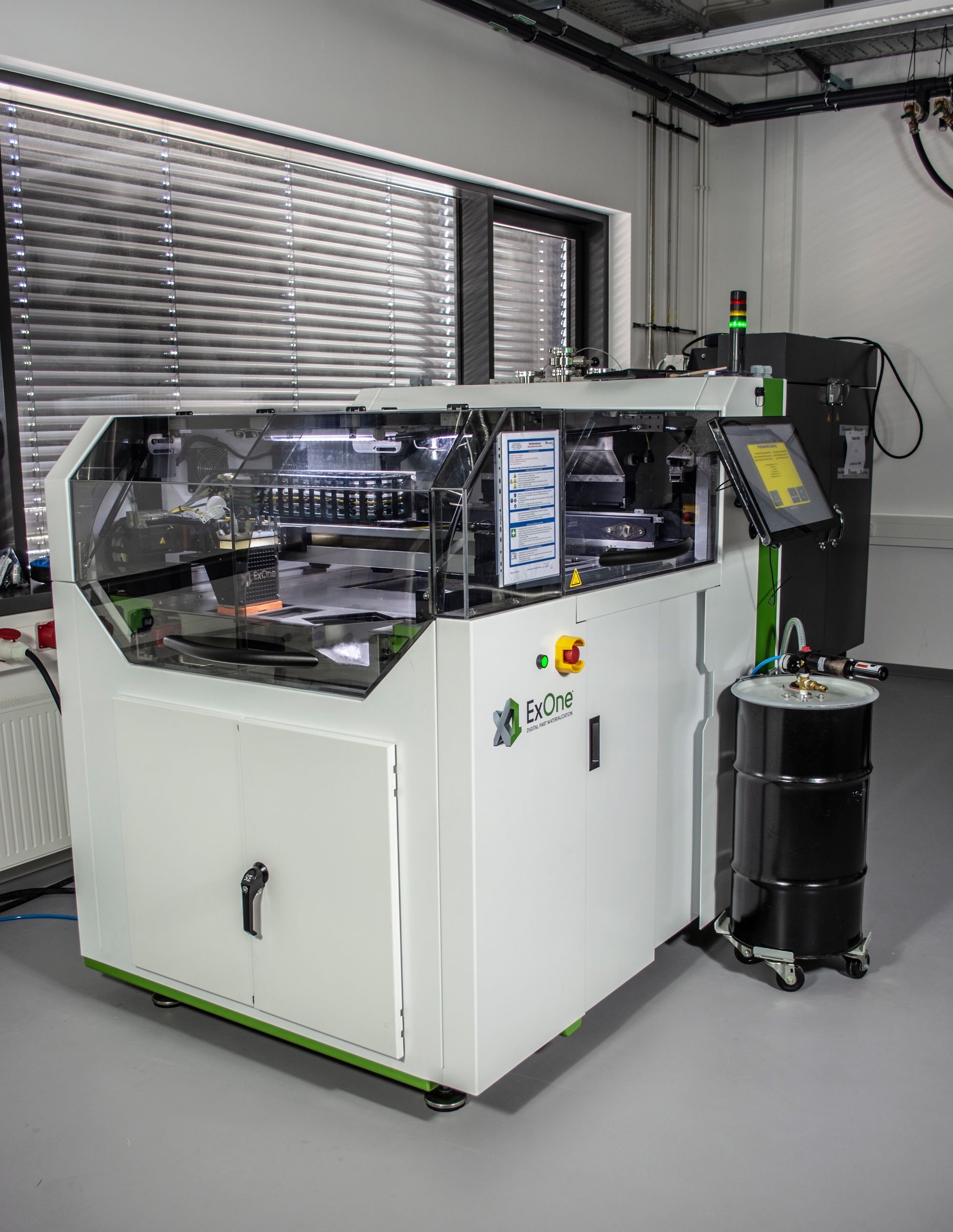
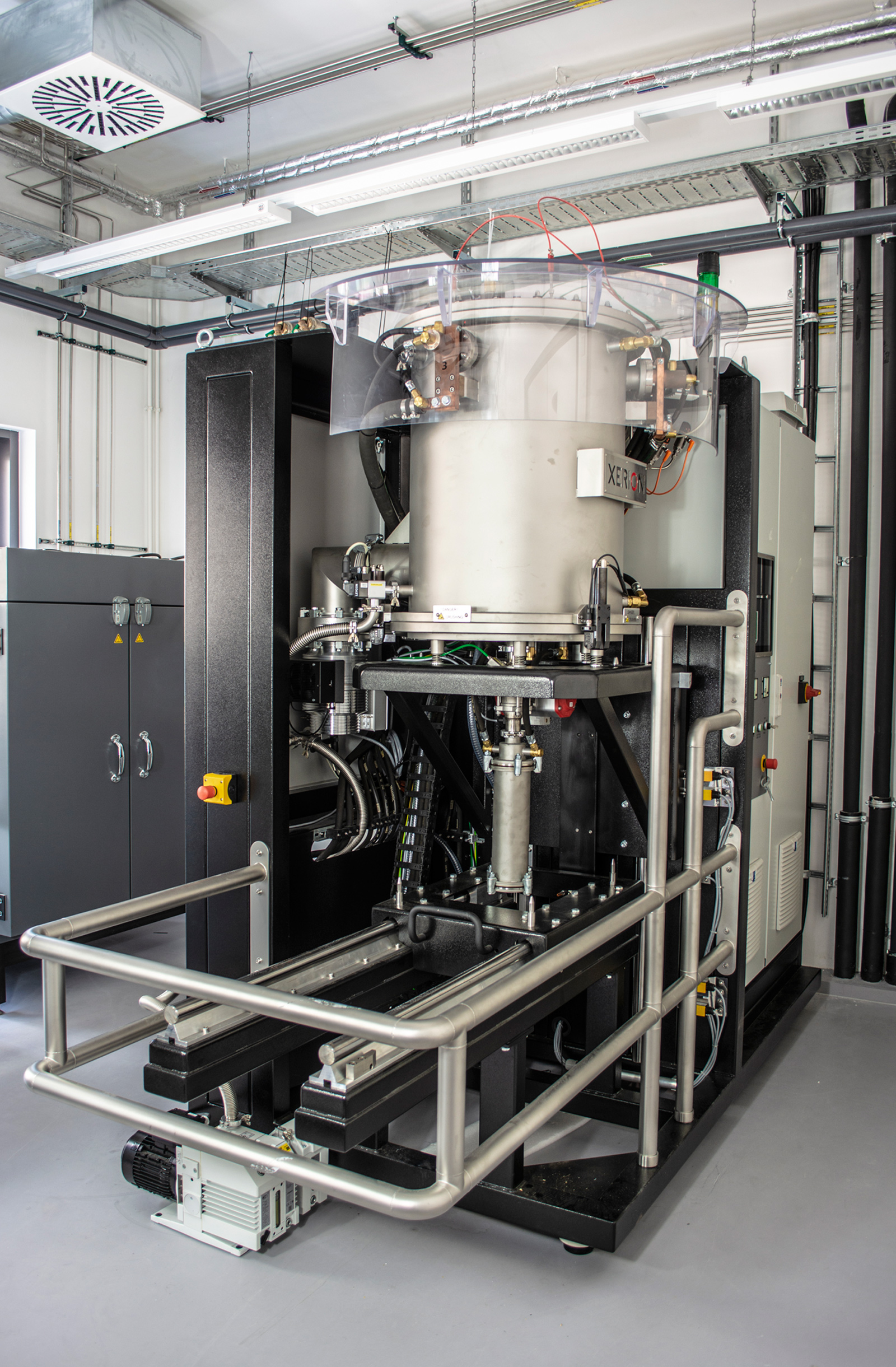
Das Fraunhofer IWS erweitert sein Nebengebäude, in dem sich unter anderem das Additive Manufacturing Center Dresden (AMCD) befindet. Auch technisch rüstet das Institut auf: Zwei zusätzliche Etagen bieten nun nicht nur einer mit einem grünen Laser ausgestatteten Fertigungsanlage und einem Binder Jetter Platz sondern auch einem neuen Kaltwandofen.
Dieser erweitert mit einem Kammervolumen von etwa 21 Litern (Ø300 mm, Höhe 300 mm) das bestehende Anlagenportfolio zur Verarbeitung von Binder-Jetting-Bauteilen. »Das im Binder Jetter eingebrachte Bindemittel muss dafür zur Weiterverarbeitung wieder entfernt und das Bauteil anschließend noch gesintert werden, um die gewünschten Werkstoffcharakteristiken zu erhalten«, erläutert Moritz Greifzu, Mitarbeiter der Gruppe »Drucken« am Fraunhofer IWS. »Der neue Kaltwandofen ermöglicht es uns nun, beide Schritte in einer Anlage vorzunehmen. Wir sparen somit Zeit und werden variabler in der Bearbeitung von 3D-Bauteilen.«
Hitze und Vakuum gleichzeitig möglich
Die Besonderheiten der Anlange besteht darin, dass sich aufgrund einer eingebauten Kühlfalle und einer speziellen Gasführung die Entbinderungase nicht an der Ofenwand absetzen oder das Bauteil kontaminieren. Dieser »saubere« Entbinderungsprozess macht eine anschließende Kammerreinigung obsolet. »Die Prozessparameter geben außerdem Aufschluss darüber, unter welchem Druck der Binder entweicht – für uns Forschende ein interessanter Aspekt«, fügt Greifzu hinzu.
Einen zweiten großen Vorteil – neben der Kühlfalle – ermöglicht die Kaltwandkonstruktion mit den verschiedenen Betriebsmodi:
- Sintern mit Gasen (Argon, Stickstoff)
- Sintern mit Wasserstoff
- Oxidation des Sintergutes wird verhindert
- Maximaltemperatur von bis zu 1850 Grad Celsius
- Breites Materialportfolio des Sintergutes, von Kupfer und Stählen über Nickel-Basis-Legierungen bis hin zu Titan
- Sintern im Hochvakuum (10-4 Millibar)
Beim neuen Kaltwandofen handelt es sich folglich um eine vielseitige Anlage, die das Maschinenportfolio für das Additive Manufacturing Centers Dresden (AMCD) um Herstellung und Bearbeitung der Binder-Jetter-Bauteile ergänzt. Neben der eigenen Forschungstätigkeit an diesen Anlagen steht der Kaltwandofen interessierten Materialherstellern oder Anwendern zu Anwendungs- und Testzwecken in der Additiven Fertigung zur Verfügung. Die Experten des Fraunhofer IWS stehen ihnen mit ihrer Erfahrung sowie ihrem Fachwissen zur Seite und beraten und begleiten sie, um gemeinsam praktische und industrienahe Lösungen auf werkstoff-, prozessrelevante und technische Fragen zu finden.
Infobox: Binder Jetting
Das Binder Jetting, ein sogenanntes Pulverbettverfahren, fertigt Bauteile Pulverlage für Pulverlage durch lokales Eindrucken eines Binders. Dieses 3D-Druckverfahren kann aus Kunststoffen, Metallen oder Keramiken komplexe Strukturen wie Wärmetauscher, Spulensysteme oder innenliegende Geometrien erzeugen. Der Binder besteht aus Polymeren und wirkt wie ein Klebstoff. Mittels einer Düse wird er nur selektiv auf die Pulverareale aufgetragen, an der das Werkstück »wachsen« soll. Anschließend wird neues Pulver in den Prozess eingebunden und wiederum nur an den notwendigen Stellen der Binder aufgebracht. So wächst nach und nach ein Bauteil, das keinerlei Stützstrukturen benötigt. Nacharbeiten, wie das Entfernen der Stützgeometrie, entfallen. |