Fraunhofer IWS erforscht funktionale Strukturen als stabile und günstige Alternativen zu manuellen Verkabelungen
Funktionale Leiterbahnen aus dem 3D-Drucker
Sicherungen, Module und Verbindungskabel kommen in den unterschiedlichsten technischen Umgebungen zum Einsatz – vom Inneren herkömmlicher Schaltschränke bis in den Weltraum reichen die Anwendungsgebiete. Während der Automatisierungsgrad in der Herstellung unterschiedlicher technischer Komponenten steigt, bleibt die Verkabelung ein aufwendiger und fehleranfälliger manueller Prozess. Forschende am Fraunhofer IWS entwickeln mit Partnern wie AIRBUS Verfahren, um Leiterbahnen günstig und sicher herstellen zu können.
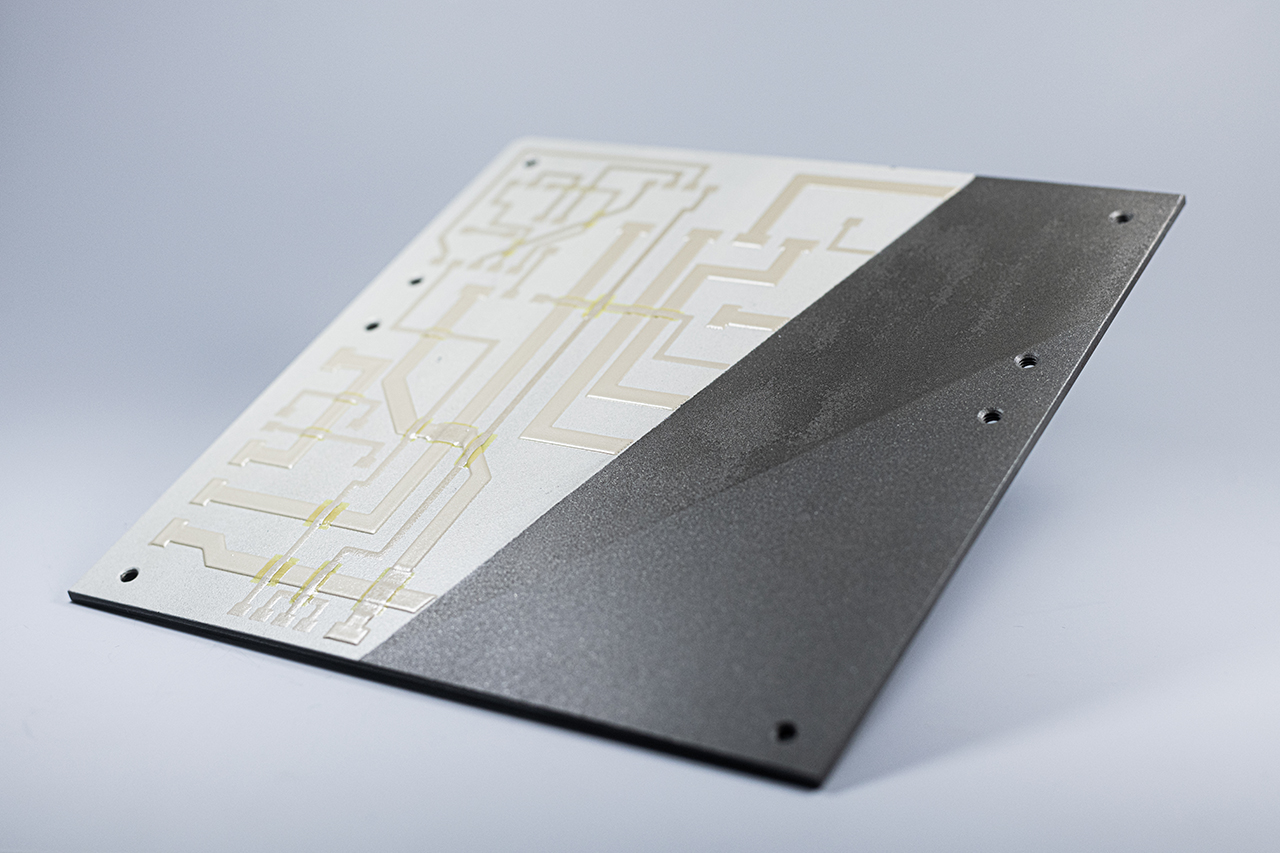
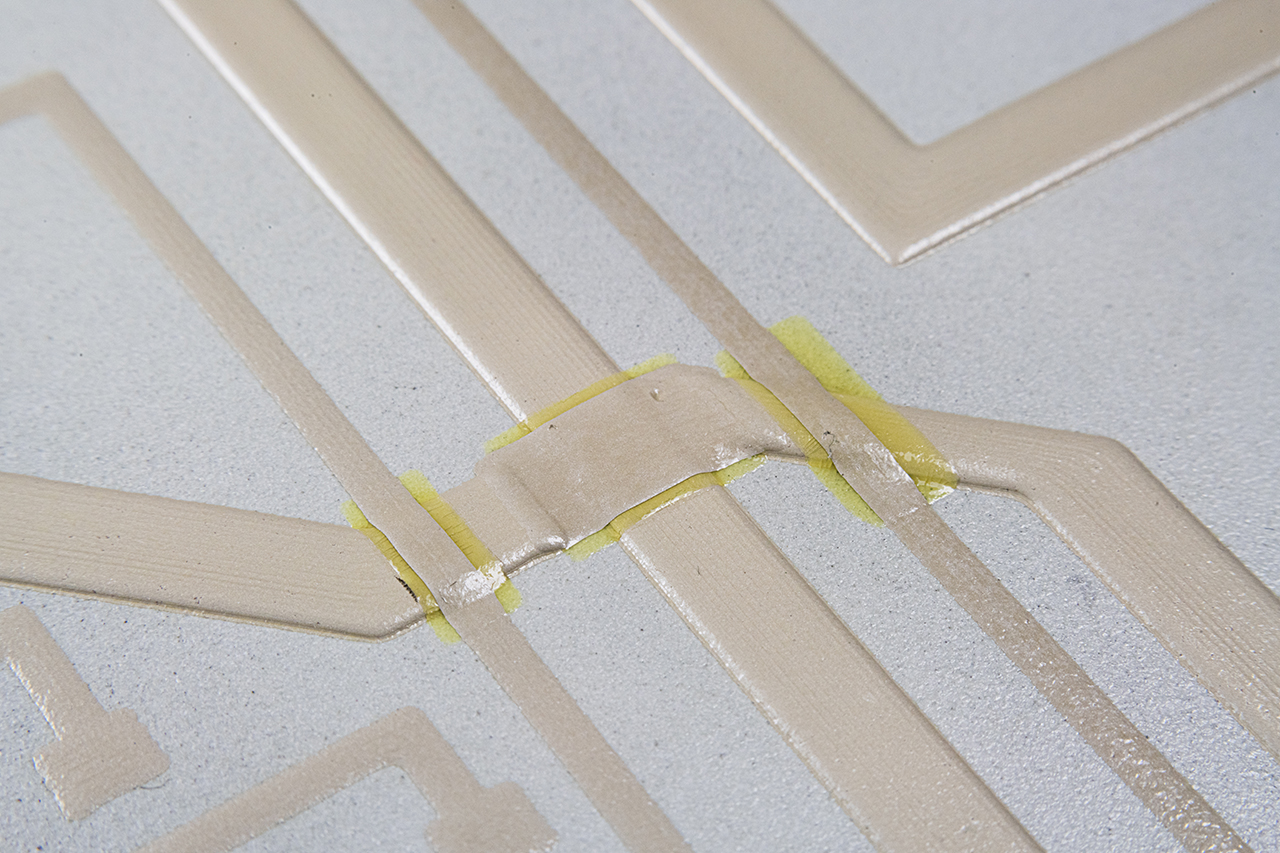
Fraunhofer IWS erforscht funktionale Strukturen als stabile und günstige Alternativen zu manuellen Verkabelungen
Moritz Greifzu gehört zur Gruppe Pulverbettverfahren und Drucken am Fraunhofer IWS. Seine Teammitglieder und er forschen in mehreren Projekten daran, funktionale Strukturen mithilfe additiver Fertigungstechnologien zu entwickeln. Ein aktuelles Vorhaben, bei dem es um das Beheizen von Materialien in der Luft- und Raumfahrt geht, treibt er gemeinsam mit AIRBUS voran. Ziel ist es, auf dem Gebiet des Thermal Engineerings Fortschritte zu erarbeiten, um die Fehleranfälligkeit bei der Integration von Heizern auszumerzen. Denn Flugkörper, die in den Weltraum entsendet werden, lassen nichts anderes als eine »Zero Tolerance« in der Fehleranfälligkeit zu. Die Projektpartner starteten kürzlich die dritte Stufe: Nachdem in einem ersten Projekt geprüft wurde, ob sich leitfähige Materialien auf Treibstoffleitungen drucken lassen und welche Heizleistung sich dabei erwarten lässt, standen in Stufe zwei raumfahrtspezifische Tests mit verschiedenen Materialien auf dem Programm, um zu erforschen wie sich bestimmte Leistungen elektrisch und thermisch erreichen lassen. Im aktuellen Projekt untersuchen die Wissenschaftler, ob die angewendeten Verfahren sich nicht nur für umrissene Referenzanwendungen eignen, sondern auch für den allgemeineren Einsatz im Thermal Engineering für Raumfahrtzeuge. So kann eine Fragestellung lauten: Wie muss unter bestimmten Einsatzbedingungen ein Heizelement ausgelegt sein?
Leiterbahnen schneller, sparsamer und einfacher drucken
Den Prozess der Verdrahtung von Bauelementen zu vereinfachen, Prozesszeiten zu verkürzen und Material einzusparen, diesen Aufgaben widmete sich die Gruppe in Zusammenarbeit mit weiteren Fraunhofer-Instituten und Industriepartnern im Projekt AGENT-elF. Konkret erforschten sie eine Methode, um Leiterbahnen für Hochleistungselektronik über einen additiven Fertigungsprozess auf eine Montageplatte zu drucken. Sie setzten sich dabei zum Ziel, Leiterbahnen mit einer Stromtragfähigkeit von sechs Ampere zu drucken.
Was hier so einfach klingt, stellt sich in der Praxis jedoch weit schwieriger dar. Denn die Herausforderung bestand darin, beim bereits etablierten Prozess des Dispensens das Zusammenspiel aller eingesetzter Werkstoffe zu gewährleisten. Dafür trugen die Wissenschaftler eine Paste, die in ihrer Konsistenz Zahnpasta ähnelt, gezielt in dünnen Bahnen direkt auf die zu bedruckende Oberfläche auf. Diese Paste enthält metallische Partikel, die durch einen thermischen Nachbehandlungsschritt eine gute elektrische Leitfähigkeit in der gedruckten Bahn erzeugen. »Gemessen werden wir an herkömmlichen Kupferkabeln«, erklärt Diplomingenieur Greifzu. »Wir müssen den Strom zuverlässig führen und die bei so hohen Strömen entstehende Wärme gut ableiten. Der Querschnitt der gedruckten Leiter ist zwar etwas größer als beim vergleichbaren Kabel, aber der direkte Kontakt zur Schaltschrankwand sorgt für eine bessere Abführung der Wärme.« Eine homogen angemischte Paste macht es möglich, die Komponenten so genau aufeinander abzustimmen, dass Druckpaste, Keramikbeschichtung und metallische Grundplatte nach dem Ausheizen eine feste Bindung eingehen, ohne dass sich die Trägerplatte unter den hohen Temperaturen des Ausheizens verzieht.
Dabei gelang es den Forschenden auch leitende und nichtleitende Leiterbahnen über Kreuz aufeinander zu drucken. Dass die Projektpartner die gesetzten Ziele erreichten, stellte ein 300 mal 300 Millimeter messender Demonstrator unter Beweis, der während des Projekts entstand. Dessen Maße wollen die Wissenschaftler in Zukunft weiter ausdehnen, um größere Vorhaben in Angriff nehmen zu können. Moritz Greifzu blickt voraus: »Das Potenzial für gedruckte Leiterzüge schätzen wir als hoch ein. Denn neben Heizfolien für die Luft- und Raumfahrt und Schaltschränken benötigen eine Vielzahl weiterer Anwendungsfelder wie etwa die Automobilindustrie Verkabelungen, die sich in Zukunft kostengünstig und stabil im 3D-Druck herstellen lassen könnten.«