Beschichtungsanlage Multi-Sputter-Lab 600 (MSL600)
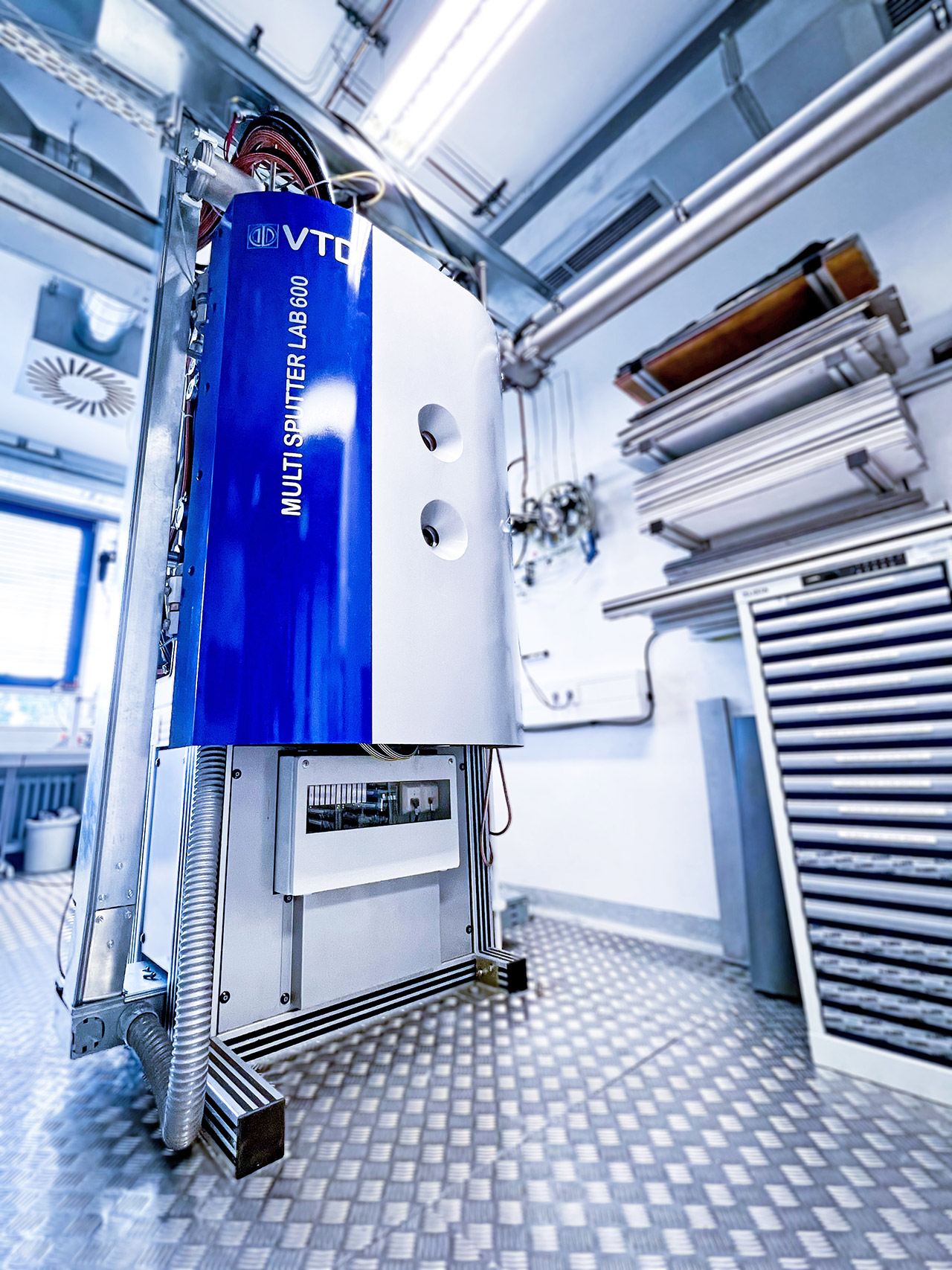
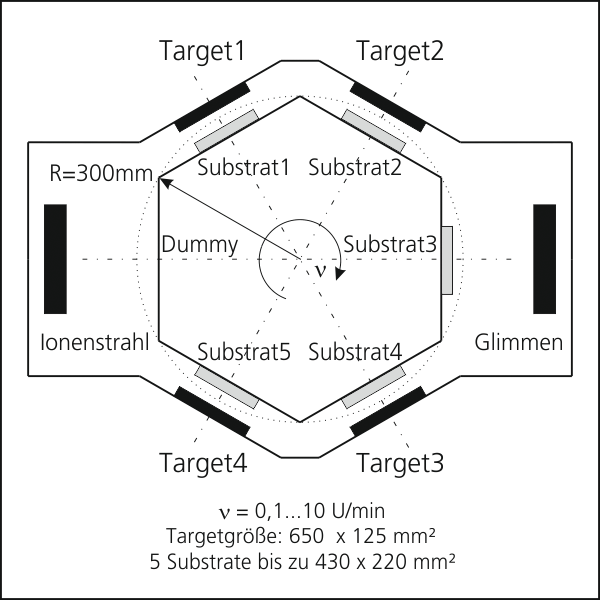
Reaktive Multischichtsysteme (RMS) werden über PVD-Verfahren, wie dem Magnetron- Sputtern hergestellt.
Das Magnetron-Sputtern bietet die Vorteile einer präzise kontrollierten Herstellung, sowie die Möglichkeit der Aufskalierung für hohe Stückzahlen. Mit der Multi-Sputter-Lab 600 (MSL600 des Herstellers VTD Vakuumtechnik Dresden GmbH) ist es möglich, sowohl freistehende RMS-Folien für mobile Anwendungen herzustellen als auch Bauteile vollflächig oder strukturiert zu beschichten.
Die MSL600 verfügt über vier Magnetron-Beschichtungsquellen, welche mit Leistungen von bis zu 10 kW betrieben werden können und zwei Substratreinigungsstationen. Neben der RMS-Abscheidung ist es somit möglich, Vorreinigungsschritte wie Glimmen oder Ionenstrahlätzen als auch die Abscheidung von Lot- und Benetzungsschichten vorzunehmen.
Auf einem mittig zu den Beschichtungsquellen angeordneten sechsfach Polygon-Substratträger können bis zu fünf Bauteile oder RMS mit den Abmessungen von bis zu 430 x 220 mm2 homogen beschichtet werden. Bei maximaler Auslastung können damit in einem Durchlauf RMS mit einer Fläche von bis zu 4730 cm2 hergestellt werden. Eine Substratkühlung sorgt für die zuverlässige Wärmeabfuhr der zu beschichtenden Bauteile als auch für eine hohe Energieausbeute der hergestellten RMS.