SNEAK PEEK: First insights in the not-yet-published Annual Report 2021/2022
ESA-ASPIRER: aerospike rocket engine with 6000 Newton thrust from the powder bed 3D printer.
Advanced thermal spraying, welding and additive manufacturing technologies are set to aid the breakthrough a highly fuel-efficient alternative rocket engine for profitable small satellite missions. The technology in question is an aerospike engine. Such engines could reduce fuel consumption by one-third for many rocket launches, thus improving the environmental and financial costs of space travel.


ESA research project develops new space propulsion systems
Unlike the classic bell-shaped rocket nozzles, aerospikes form an annular gap between the spike and the shell to efficiently convert the hot exhaust gases into thrust. Aerospikes are thus better able to adapt to the atmospheric pressure in different altitudes and keep the gas exit jet close to its ideal shape, regardless of the ambient pressure. Aerospikes were first developed more than 60 years ago. However, their practical use failed due to their complexity and the demanding manufacturing process. The complex internal cooling channels for such engines can hardly be produced using traditional methods. The Institute of Aerospace Engineering (ILR) at TU Dresden and Fraunhofer IWS have been closely collaborating since 2016 and have already designed, manufactured and tested a 500 Newton aerospike in 2019. However, problems with the cooling system and fuel injection still emerged. Since 2020, the European Space Agency ESA has been funding the ”AeroSPIke Rocket Engine Realisation” (ASPIRER) project. As a result, the cooperation of Fraunhofer IWS researchers with ILR, the “Space Technologies Center – Lukasiewicz Research Network“ from Warsaw and the “ArianeGroup“ from Munich enters the next round.
Use of laser for generating and joining
Samira Gruber, Alex Selbmann and Michael Müller from the Additive Manufacturing group use powder bed-based laser beam melting to manufacture the two core components, the stinger and the combustion chamber outer wall. For this purpose, the laser system melts a nickel-based super alloy in metal powder bed and creates the components layer by layer. Important interface surfaces are mechanically machined and the injector holes are eroded to maintain necessary tolerances. Subsequently, the scientists of the Thermal Spray team, deposit a ceramic heat protection layer on the thermally stressed surfaces. This prevents the core material from melting later due to the hot gases during takeoff and the flight phase. Finally, a further Fraunhofer IWS team joins the spike and the shroud via laser welding. The engine should be ready by beginning of 2022. In March 2022, the partners want to start an extensive test campaign in Poland.
Review Hannover Messe 2021: Additively manufactured rocket engine with aerospike nozzle – from conceptual design to realization
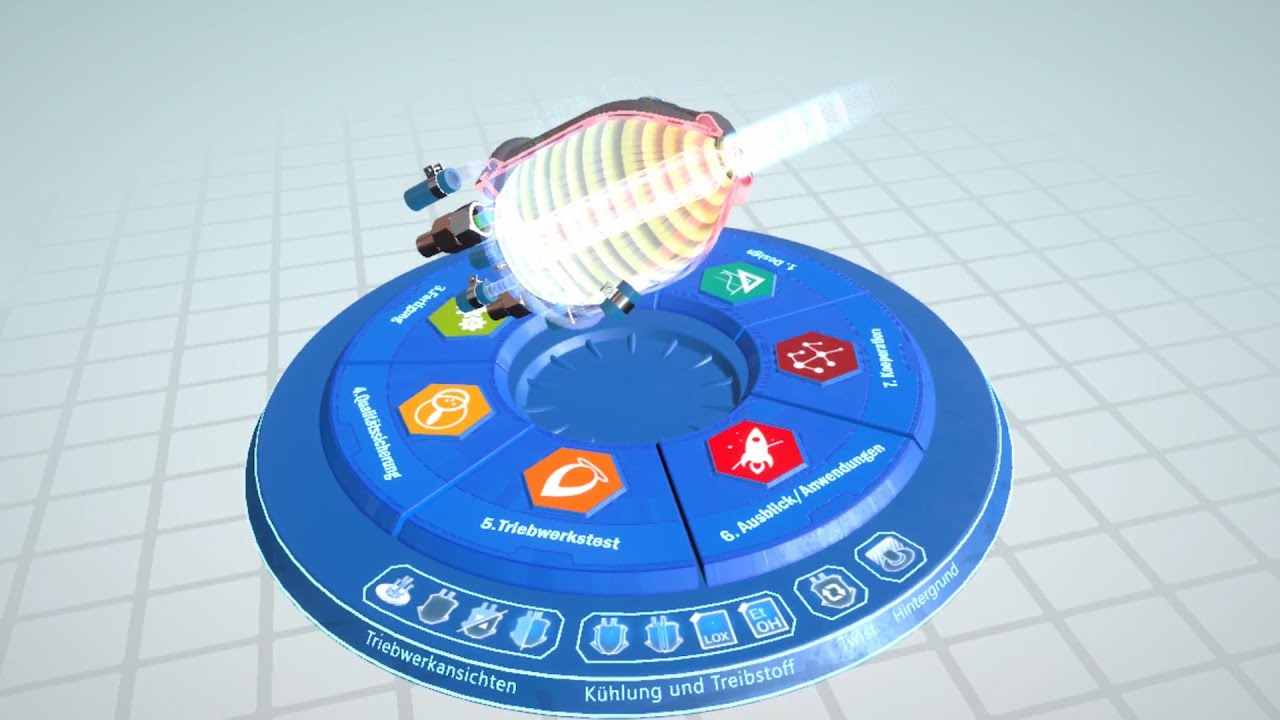
Privacy warning
With the click on the play button an external video from www.youtube.com is loaded and started. Your data is possible transferred and stored to third party. Do not start the video if you disagree. Find more about the youtube privacy statement under the following link: https://policies.google.com/privacyVideo: Additively manufactured rocket engine with aerospike nozzle – from conceptual design to realization (YouTube)