First Successful Test of a Generatively Manufactured Aerospike Engine Using Hydrogen Peroxide-Kerosene Propellant
Innovative Hot Gas Test: A Milestone for Aerospike Engines
A consortium comprising Fraunhofer IWS, the TUD Dresden University of Technology, ArianeGroup, and the Warsaw Institute of Aviation has achieved a significant breakthrough in aerospace engineering: the first successful hot gas test of a 3D-printed aerospike engine powered by a combination of sustainable hydrogen peroxide and kerosene propellant. This project was conducted under the ESA-funded ASPIRER initiative. The test results hold the potential to enhance the efficiency of space missions significantly.
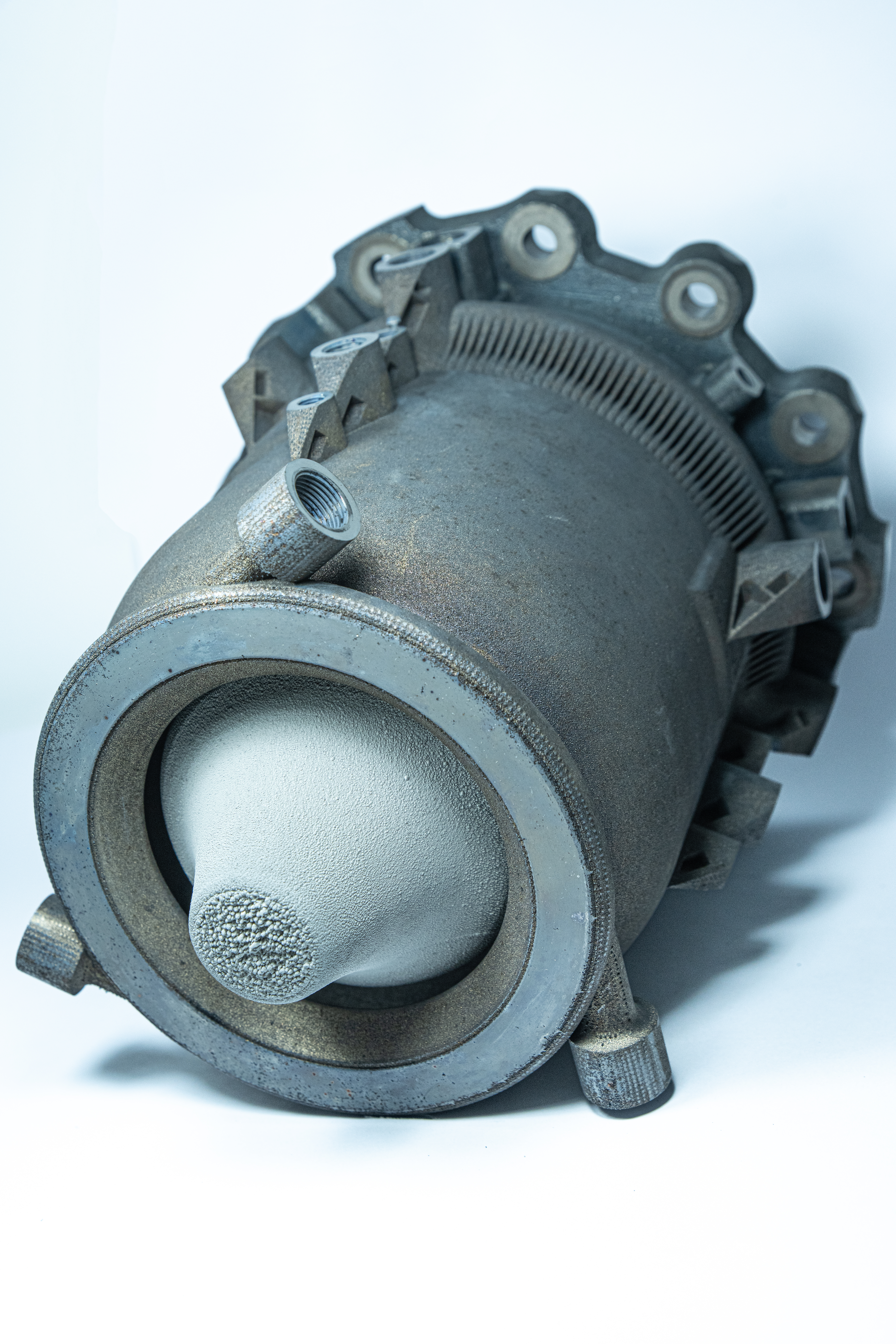
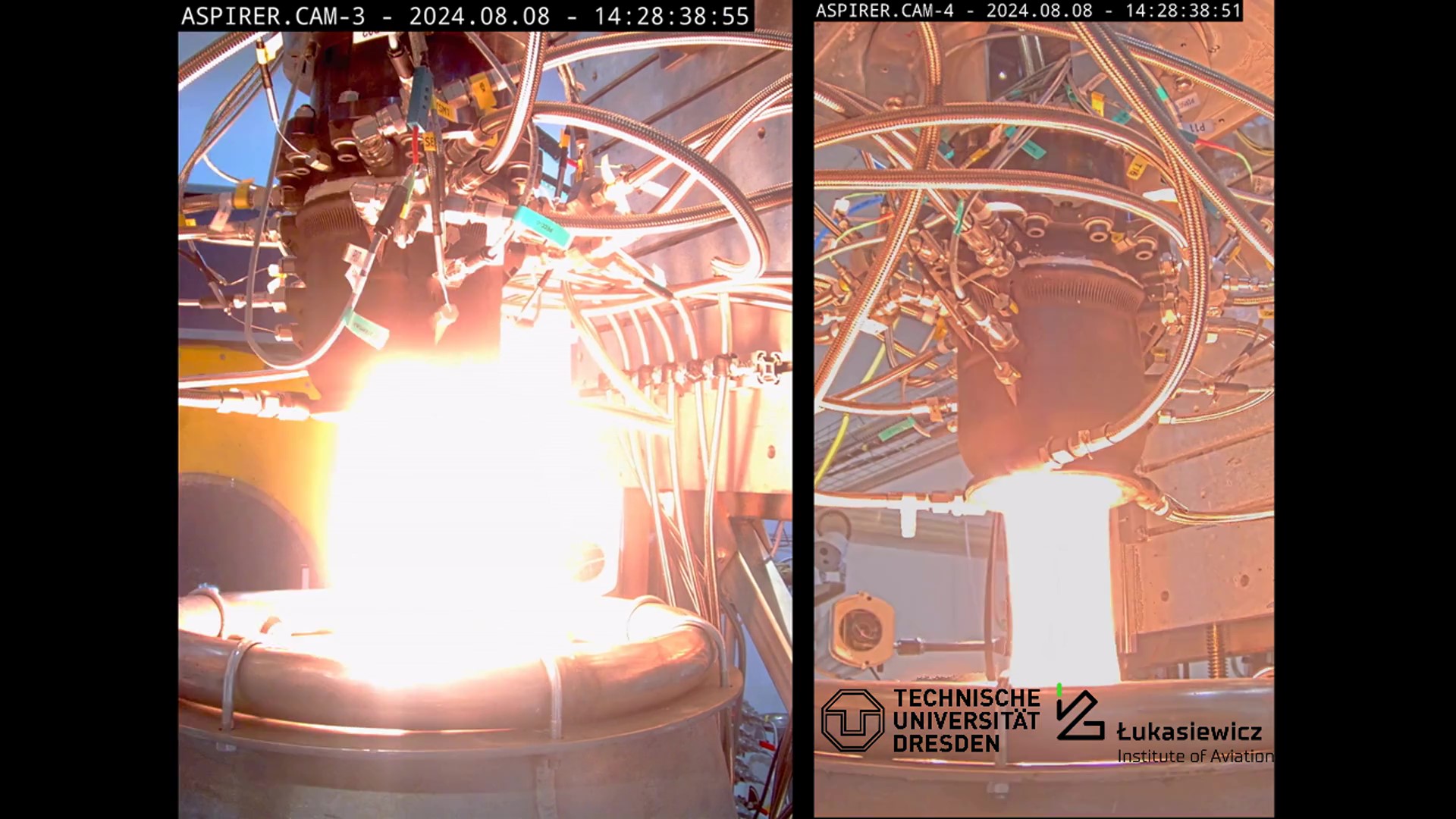
Aerospike engines are technically fascinating and offer substantial advantages over conventional bell nozzle rocket engines. While traditional engines are often limited by their high fuel consumption and due to lower efficiency, aerospike engines deliver superior performance across various altitudes. These characteristics position them as a promising solution for future space missions, particularly when sustainability is becoming increasingly critical.
Challenges and Solutions: A Breakthrough Through Additive Manufacturing
The complexity of aerospike engines poses considerable challenges, especially regarding cooling, which is crucial for managing the high thermal loads inherent to their operation. “Thanks to innovative 3D printing techniques like selective laser melting, we were able to implement internal cooling solutions,” explains Samira Gruber, project lead at Fraunhofer IWS. These cooling solutions are essential for regulating combustion chamber temperatures and ensuring the engine’s safe operation.
By combining selective laser melting with a newly developed heat-resistant ceramic coating for combustion chamber components, the scientists contributed to successfully executing the hot gas test. The project team also developed a comprehensive process chain encompassing additive manufacturing and subsequent processing steps like milling and laser welding. This integrated approach allows for efficient design modifications while ensuring the engine’s overall quality. “Our tests confirmed that the entire manufacturing process worked as intended. Everything held up as designed,” notes Alex Selbmann, a research associate at Fraunhofer IWS who oversaw the entire process chain.
Efficiency and Sustainability: The Future of Spaceflight
Aerospike engines offer significantly greater fuel efficiency than conventional rocket engines and feature a lighter, more compact design. These attributes make them ideally suited for various mission scenarios, including launch vehicles, expeditions to Mars and Saturn’s moon Titan, and lunar landers. “In the case of lunar landers, aerospike engines could represent a more sustainable alternative to conventional hydrazine-based propulsion systems,” emphasizes Gruber. Traditional propellants are increasingly scrutinized due to health and environmental risks, emphasizing the importance of developing greener alternatives.
The distinctive shape of aerospike engines also enables greater design flexibility, leading to flatter lunar landers that facilitate easier loading and unloading by astronauts and the deployment of rovers. The combination of efficiency, sustainability, and cutting-edge technology places aerospike engines as a forward-looking solution for space exploration. Furthermore, using these engines in various applications could help reduce the aerospace sector’s carbon footprint and lower operational costs.
Looking Ahead: Alternative Propulsion Systems for Space Exploration
Fraunhofer IWS’ developments aim to assess the suitability of alternative propulsion control methods and, in the long term, advance aerospike engines’ technological maturity. Research will focus on developing innovative control systems to optimize engine performance under diverse conditions. Overcoming the uncertainties associated with these technologies could pave the way for a new era of environmentally friendly propulsion systems in future space missions. “We are confident that our approaches have the potential to transform the space industry sustainably,” concludes Gruber.
In addition, Fraunhofer IWS will continue refining manufacturing processes to reduce production costs and increase the availability of these innovative engines for upcoming missions. The vision is clear: a sustainable and efficient space travel for generations to come.
Since 2020, the European Space Agency (ESA) has been funding the project "AeroSPIke Rocket Engine Realisation" (ASPIRER) with the involvement of ILR as the consortium leader, Fraunhofer IWS, the "Space Technologies Center – Lukasiewicz Research Network" from Warsaw, and ArianeGroup.