Numerical simulation and calculation for developing structurally relevant products
Simulation and manufacturing working closely together
In the course of the digital revolution, numerical simulation and calculation methods are taking on a decisive role in all product lifecycle stages. In order to develop structurally relevant products for the automotive and aerospace industries as well as for medical and energy technologies, it is necessary to have a holistic strategy with particularly close inter¬linking between virtual and real worlds.
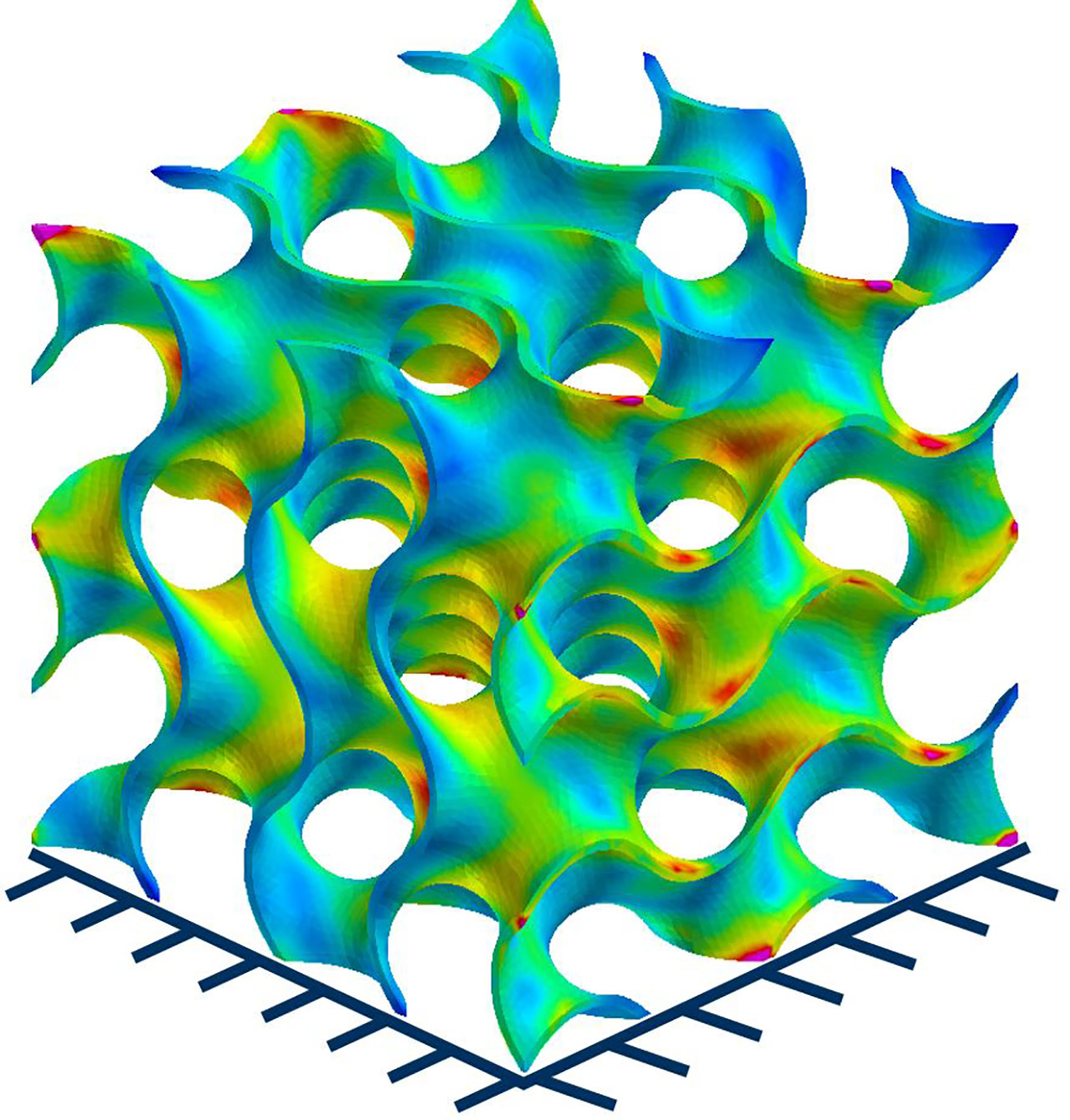


Numerical simulation and calculation for developing structurally relevant products
“Product developments within structural mechanical applications are currently hardly imaginable without numerical simulations,” says Dr. Markus Wagner, group lead of the group Component Design and Special Technologies at Fraunhofer IWS. The simulation results' quality strongly depends on understanding the material- and process-specific parameters.
With this intention, his newly founded focuses on a particularly close link between simulation, process development and component testing in order to develop tailored all-in-one solutions for tomorrow's industry.
A collaboration for realistic and ecological models
The close cooperation with process development and materials engineering experts makes possible the generation and analysis of realistic simulation models. The research field concentrates on efficient joining technologies for metallic and non-metallic hybrid structures, such as laser beam and friction stir welding, magnetic pulse joining, structural adhesive bonding, direct thermal joining, and a wide range of innovative additive manufacturing technologies. In addition, the ecological use of resources represents a further priority in the development of future-proof concepts and manufacturing technologies. "We primarily address the automotive, aerospace and medical industries. We also focus on the mechanical engineering and energy and environmental industries," Dr. Markus Wagner lists.
Application-related focal points for the close cooperation between simulation and manufacturing are:
- Development, manufacturing and testing of laser-welded powertrain components for automotive electric and combustion engines as well as for aerospace applications
- Holistic processing of joining tasks for material and form-fit joints between conventionally difficult-to-weld and between different materials by means of friction stir welding (FSW) and magnetic pulse welding (MPW)
- Numerical simulation and design of additively manufactured bone implants featuring optimized biomechanics performance and biocompatibility based on the triple-periodic minimal surface (TPMS) principle
- Holistic development of process-, material- and stress-optimized design solutions for lightweight body structures all the way to large welded components for steel construction and the energy sector