Joint Project “H2GO” Aims to Revolutionize Production of Mobile Fuel Cells
Carbon instead of Gold: On the Road to Zero Emission Heavy Duty Vehicles
Powerful mobile fuel cells can help to reduce the environmental impact of heavy duty transportation in Germany and worldwide in the future. 19 Fraunhofer Institutes from nine German states have therefore joined forces to form the development alliance “H2GO – National Fuel Cell Production Action Plan”. They aim to jointly develop industrial technologies to produce fuel cells and efficiently transfer new processes to industry. The focus is on fuel cells for road-based heavy duty vehicles. The Federal Ministry for Digital and Transport Affairs is funding H2GO with around 80 million euros from the “Future Fund for the Automotive Industry“ until the end of 2025. The Fraunhofer Institute for Material and Beam Technology IWS is also part of this consortium. Dr. Teja Roch oversees the “HP2BPP” sub-project at Fraunhofer IWS, located in Dresden and Dortmund. In this interview, he explains the innovative contributions.
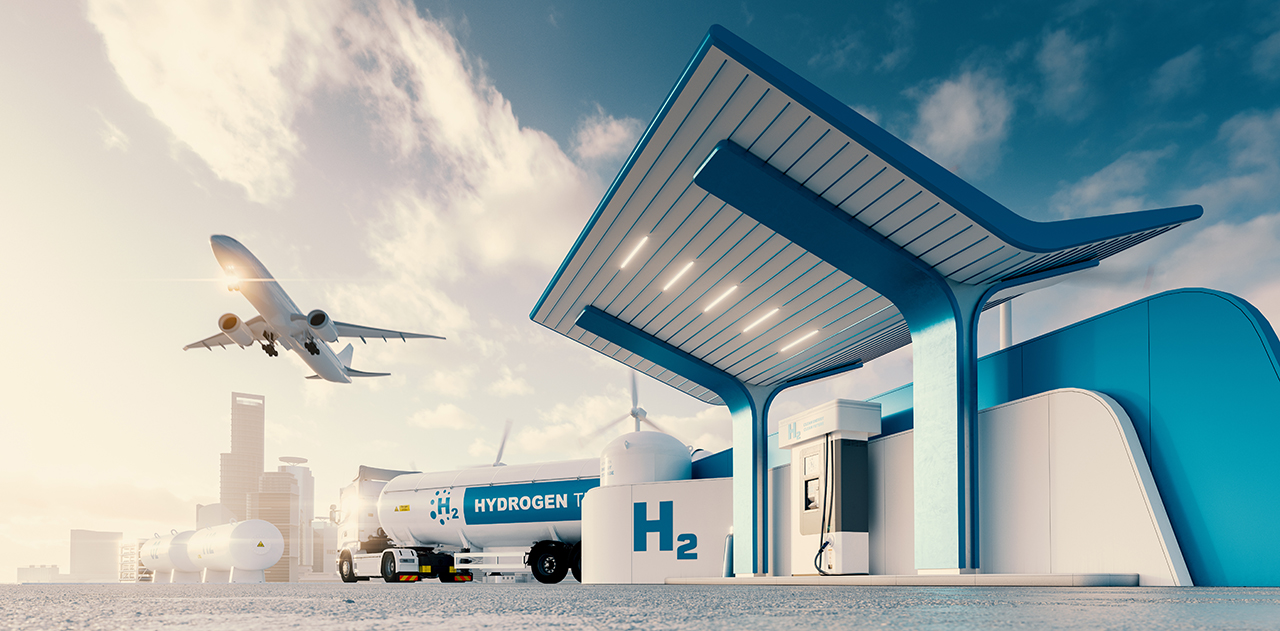
Fuel cells consist of many components. Which components and processes are you focusing on in the H2GO network?
Dr. Teja Roch: Together with other Fraunhofer institutes, we are working on systems that can manufacture bipolar plates for fuel cells remarkably quickly and efficiently using a roll-to-roll process. A bipolar plate is an important component of a fuel cell stack. Hydrogen and oxygen are introduced through channels and the plates are also responsible for the electrical connection between the individual cells of a fuel cell stack among other functions. So far, only a few continuous manufacturing processes have been established for their production. The plates have to be formed from metal sheets and cut to size. In the following, two halves are joint together, coated, and stacked with other components. We want to automate and accelerate these production processes to a greater extent and also use new coating materials.
How can we imagine this new generation of systems when they are ready for series production in the next few years?
Dr. Teja Roch: The process involves the following sequence: a stainless steel band is fed from a coil through air-vacuum locks into a coating system with multiple chambers for a physical vapor deposition (PVD) process. The steel is first cleaned and coated with a metallic corrosion protection layer, which also improves the adhesion. In a further PVD chamber, a conductive carbon layer is deposited onto the steel band. Subsequently, forming processes follow to emboss the channels for the gas flows into the coated band. The system then joins the metal band and separates the individual plates.
One innovation represents the conductive carbon layer which is only a few nanometers thick. This can replace alternative thicker layers or precious metal coatings, e.g., gold. This offers the potential to significantly reduce the production costs for fuel cells and even increase electrical efficiency. We are testing a chromium and other layers made of titanium or special alloys for corrosion protection.
What specific tasks has Fraunhofer IWS taken on during H2GO?
Dr. Teja Roch: In the HP2BPP sub-project we focus on coating technologies, including the processes and quality control. Other tasks include joining processes like bonding or laser roll welding, as well as separation by high-speed laser cutting of the bipolar plates. The consortium leader, Fraunhofer Institute for Machine Tools and Forming Technology IWU, is responsible for other sub-steps, such as the forming.
What stage have you reached, and where do you want to go?
Dr. Teja Roch: We have made significant progress in the development of coating, cutting and joining processes of bipolar plates in recent months. We have now developed a system concept for coating of 100-micrometer thin and 300-millimeter wide steel strips, which will be installed in 2024. In the future, we also want to develop concepts for 50- to 75-micrometer thin and wider strips at higher speeds of up to 60 meters per minute. Additionally, we have demonstrated the fundamental feasibility of innovative joining processes using laser gap welding and seal bonding and have developed system concepts for this purpose that are currently being realized. To ensure that such systems offer real added value for system manufacturers, we want to accelerate them to a cycle rate of more than one bipolar plate per second.
What challenges need to be overcome on the way there?
Dr. Teja Roch: In addition to the overall system design, many detailed tasks need to be solved. One example is the design of the carbon evaporators for the PVD chambers. We have now developed a linear evaporator concept for this purpose, but we also continuously improve established concepts, such as the laser arc process, as an alternative solution. This topic will be one main focus of our work not only in 2024 but also in the future. There are also signs of significant progress in the laser-based joining processes we use to assemble a bipolar plate from two half-shells. For example, we have to develop multi-beam laser optics in smallest installation spaces. We may be able to report some news on this soon.
In addition, we continue to work on better air-vacuum locks, which must ensure a scratch-free transition into the vacuum chambers. We are also still making many adjustments to further increase our process speed, implement inline quality assurance and be able to offer smart processes overall in the future.
Why is H2GO so important?
Dr. Teja Roch: We develop the production technology for tomorrow and the day after tomorrow. Suppose manufacturers can produce compact fuel cells for mobile use more cheaply and efficiently in the future. In that case, this will also contribute to freight forwarders and other fleet operators using trucks with such environmentally friendly drive systems. This would bring us an important step closer to the goal of low-emission or even emission-free heavy duty transport.
Is the process only of interest to manufacturers of fuel cells, or are other fields of application also emerging?
Dr. Teja Roch: We must not forget that bipolar plates are not only needed for fuel cells but also for other hydrogen technologies. They could also influence the series production of electrolyzers positively in the future and reduce their costs.
Dr. Teja Roch studied physics at TU Dresden and completed his doctorate on the nanostructuring of amorphous carbon thin films. At Fraunhofer IWS, he heads the project group at Dortmunder OberflächenCentrum DOC.
Video: Cost-Efficient Strip Processes for the Production of Bipolar Plates for Fuel Cells (CONTIbip)
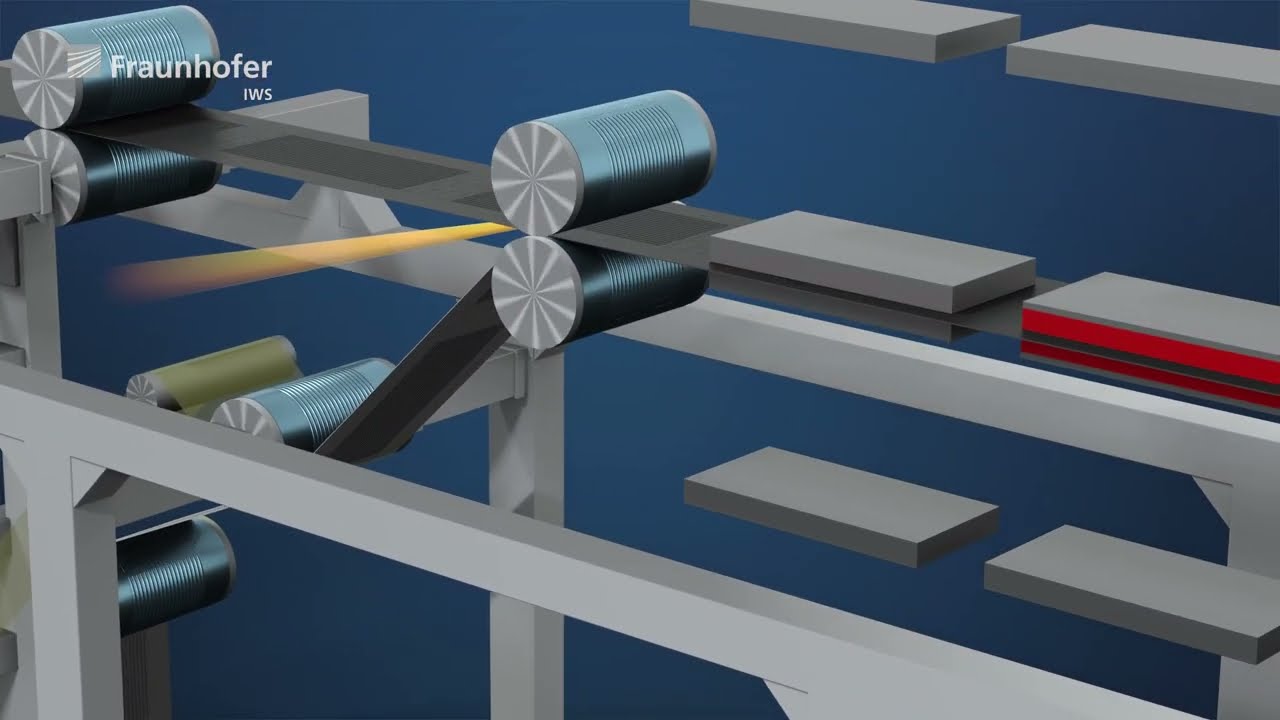
Privacy warning
With the click on the play button an external video from www.youtube.com is loaded and started. Your data is possible transferred and stored to third party. Do not start the video if you disagree. Find more about the youtube privacy statement under the following link: https://policies.google.com/privacy© Fraunhofer IWS