"contilas" cuts airbags worldwide
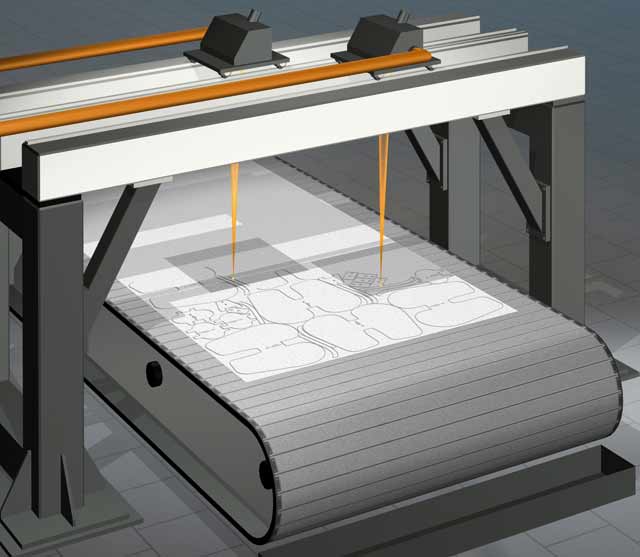
Fraunhofer IWS Dresden, in cooperation with the Held Systems company, transferred four "contiLAS" airbag laser cutting systems to internationally leading safety solutions producers for automotive applications in the last year. For this purpose, researchers customized the process and the software for the final users’ requirements and qualified them for worldwide use. The systems primarily are tasked with reliably cutting so-called one-piece-woven airbags (OPW). Woven in a single piece, OPWs are distinguished by being flat material on one side and having recessed cavities on the other. In conjunction with a suitable coating, the technique allows the airbags to take in more air. Cutting by means of laser technology has the advantage that the edges interfuse and simultaneously prevent the so-called taking off the warp.
The challenge was to identify the positions at which the system should place cuts. The partners decided to employ remote cutting, for which Fraunhofer IWS created both the concept and the triggering software. The hardware consists of a conveyor over three meters long, on which the material is cut and removed from the manufacturing zone. The principle behind: two scanners travel across the feed to extend the working zone of the laser beams. The cut contours are segmented by means of CAM software created at Fraunhofer IWS. The CAM system enables segmenting the contour and optimizes its cutting sequence to obtain maximum output. In remote processing, the laser beam is refracted by means of moving mirror elements and guided over the component to be processed with the maximum dynamics possible. This reduces the positioning times from one processing step to the next to a minimum, and the process speed remains high even for complex geometries. The laser spot speed can achieve several meters per second, so that material processing itself, such as cutting complex airbag parts, finishes within a few seconds.
IWS researchers developed and customized processing optics and software solutions for industrial remote technologies. They made them available for welding, cutting, cleaning, and engraving. Compact, powerful system solutions are created through a combination of the remote technology of rapid beam movement with a continuous material feed, for instance a several meter-wide fabric panel.